3/25/2022
BY: CHUCK WERNER
As time goes on, we continue to see more and more advanced technology in every aspect of our lives. So why not take advantage of technology within our manufacturing companies? As we work to improve efficiencies, fill talent gaps, increase profitability and stay competitive, a strategic advantage can be found in applying relevant advanced manufacturing technologies.
BUSINESS OPTIMIZATION
After implementing Enhanced Operations Management, Human Machine Interaction and Digital Process Control, we are in the predictive phase of business development. This is when we have standardized work throughout the organization, abnormal results are quickly and culturally responded to, rework/reinspection is minimized, and best practices have been applied across the board.
When this occurs, we are doing well and seeing the positive impact that Industry 4.0 has had on our company so far. However, we still have room for optimization through designs, processes and product improvements. These advanced technologies have changed the way businesses design, test, manufacture and service products. So, we need to learn how to continuously improve these areas of operations, complete with ROI calculations and expected benefits of implementation.
MAXIMIZE YOUR PROFIT
We know that our total profit is our revenue minus the cost. This means that the greater the cost of materials, labor and burden, the smaller our profit is. To maximize our profit, we need to increase sales and decrease cost.
Development costs are the activities that improve or create processes, products or services for a business to sell which include:
-
Research and data collection
-
Product/process design
-
Development of requirements and testing
-
Design modifications
-
Prototyping
-
Validation testing
-
Design and construction of tooling
To keep these costs low, we need to eliminate waste, innovate in a way that provides customer value, ensure and improve product quality, and reduce the lead time of the development cycle. This can be done through Lean Manufacturing and the technologies to support those principles.
There are also production costs, which are the costs incurred when a company produces a product or provides a service. This can be direct (materials and labor) or indirect overhead costs (rent, shipping, utilities).
EDUCATIONAL NEEDS
It’s important to note that when implementing new technologies of any kind, we need to train our employees and ensure we have the right team members in place to keep operations running efficiently. Within technology revolutions, we need five essential elements for the change to happen.
-
Vision – the ability to think about how implementing change can improve the situation
-
Skills – the expertise needed to support the vision
-
Incentive – the motivation to get it accomplished
-
Resources – having the right materials, staff, data, etc. to accomplish the task
-
Action Plan – a detailed approach, including a charter, resources, dates and milestones
These five steps are imperative when implementing these advanced technologies into your company. By creating a path for success, your staff will feel confident, prepared and motivated to be successful.
ADVANCED MANUFACTURING TECHNOLOGIES AT THE CENTER
Learn more about the benefits of Advanced Manufacturing Technologies by registering for an upcoming class at The Center. You will gain an understanding of how Industry 4.0 technologies have changed the way businesses operate. Find a class
here and learn about The Center’s additional Industry 4.0 training offerings
here.
MEET OUR EXPERT: Chuck Werner, Manager Operational Excellence/Lean Six Sigma Black Belt
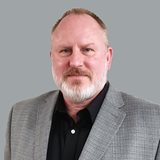
Chuck has been a member of the team at The Center since 2016. His areas of expertise include Lean, Six Sigma and Quality. Chuck has devoted many years to practicing Six Sigma methods, ultimately earning a Six Sigma Master Black Belt in 2011. He is passionate about helping small and medium-sized manufacturers become more prosperous using a variety of tools and methods gathered from over 27 years of experience in manufacturing.
Since 1991, the Michigan Manufacturing Technology Center has assisted Michigan’s small and medium-sized businesses to successfully compete and grow. Through personalized services designed to meet the needs of clients, we develop more effective business leaders, drive product and process innovation, promote company-wide operational excellence and foster creative strategies for business growth and greater profitability. Find us at www.the-center.org.
Categories: Advanced Manufacturing,
cybersecurity,
Industry 4.0,
Innovation,
Manufacturing,
Smart Manufacturing,
Technology