10/7/2022
BY: ROB STAUFFER
Most manufacturers are facing inflation, which drives up the cost of just about everything they buy. At the same time, the price of petroleum has risen, increasing the cost of transporting items to and from their factories. The current talent and workforce shortage, particularly in manufacturing, has caused an upward pressure on wages. And to make things even more challenging, many economic indicators are predicting a looming recession, which tends to shrink consumption and slow down production.
In the face of these cost challenges, here are a few things to consider:
-
ENLIST THE HELP OF YOUR MANAGERS
If your managers oversee what activities occur in their areas and how they are performed, then they have a direct impact on the costs of your business. This may sound obvious, but the difficulty often lies in the fact that many managers do not know how to read an income statement or balance sheet.
Many people also work in businesses where the finances are not shared, which means managers often make decisions by ‘feel’. If managers don’t know what is happening with company finances, their ability to help is severely limited. Trying to feel your way out of today’s challenges is avoidable, but only if financial results are shared and understood. A simple
financial class about how to read an income statement and balance sheet would be a minimal investment that could help identify opportunities for cost control and reduction.
-
HELP MANAGERS UNDERSTAND COSTS AT THE ACTIVITY LEVEL
All manufacturing companies have resources they use to make products their customers want. Examples of resources are people, building space, machines, utilities, vehicles and maintenance. Resources are then consumed by activities, such as selling, purchasing, receiving, cutting, machining, assembly, inspection and shipping. Most companies do not have a way to measure their costs at the activity level because a general ledger is not designed to give you those answers.
An activity-based costing model can be developed to answer the question of what activities really cost and (most importantly) where and why they may be too high. As mentioned in item 1, managers generally control what activities happen in their areas and how they are performed. If they could be made aware of the cost implications of doing things the way they are currently being done, they can help execute strategies to eliminate and streamline activities that consume too many resources.
-
TEACH MANAGERS TO SEE WASTE ON BOTH THE CARPET AND CONCRETE SIDES OF YOUR BUSINESS
Lean manufacturing focuses on the eight types of waste in any process. The acronym DOWNTIME is often used to describe these wastes (Defects, Overproduction, Waiting, Non-Utilized Talent, Transportation, Inventory, Motion and Extra Processing).
Many companies have accepted that there is waste in their factory, yet if you ask the floor managers what the eight types of waste are, which one is the biggest issue in their area, and what are they doing about it, they often don’t know. To compound the issue, most managers in the office have not embraced the idea that there is also waste in every office (sometimes more than in the factory).
Many companies must double the cost rates of their machines to cover the costs of the office, which is a huge opportunity for cost reduction. This sounds like a simple suggestion that would not cost much but training your managers and team members in a
Lean manufacturing and/or Lean office class would be a way to help managers identify and eliminate wasteful (and therefore expensive) activities.
My parting advice to most clients is if I owned their business, I would require everyone to know the eight types of waste and I would walk around daily to ask managers what wastes they have identified and what they are doing about it.
COST MANAGEMENT AT THE CENTER
The Center’s experts are here to help manufacturers ensure they are accurately estimating production costs when delivering quotes. We can diagnose various costing problems, tackle areas of high cost and develop implementation plans for waste and cost reduction. Learn more about
The Center’s costing services here.
MEET OUR EXPERT:
Rob Stauffer, Senior Lean, Costing & Project Management Consultant
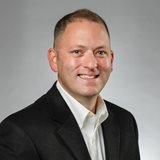
Rob Stauffer has been a Program Manager in The Center's Lean Business Solutions program for 15 years. He has trained and mentored Michigan companies in the entire portfolio of Lean Sigma strategies and methods specializing in financial analysis, costing, strategic planning, and project management. He also works with clients on product development, product launches, transactional office processes and sales of technical programs.
Since 1991, the Michigan Manufacturing Technology Center has assisted Michigan’s small and medium-sized businesses to successfully compete and grow. Through personalized services designed to meet the needs of clients, we develop more effective business leaders, drive product and process innovation, promote company-wide operational excellence and foster creative strategies for business growth and greater profitability. Find us at www.the-center.org.
Categories: Data & Trends,
Finance,
Lean Principles,
Manufacturing,
workforce,
Workplace