6/23/2017
BY: CHUCK WERNER
When teaching a new group of Continuous Improvement (Lean and/or Six Sigma) students, it’s always critical to emphasize the importance of the first “team” activity of any project or kaizen— the process map.
There are many benefits to process mapping. One is its highly visual nature. The ease of comparison between what we THINK happens and what actually does is another. It also helps to focus on what area(s) of the process are contributing to the problem or performance of the process. To illustrate the first and potentially most impactful output of the process map, let’s consider a very old, well-known story.
The Blind Men and the Elephant
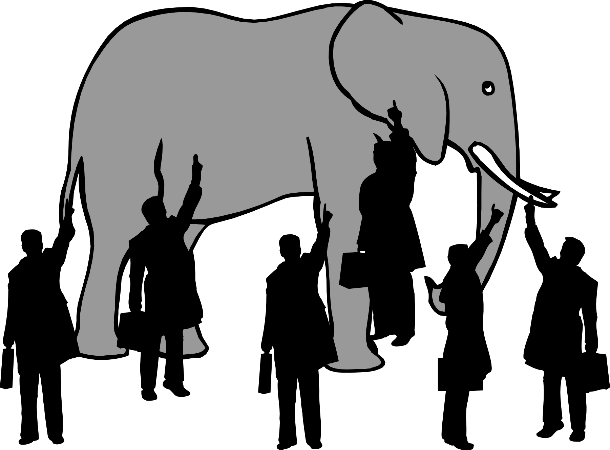
Six blind men once lived in a village. One day, they heard that there was an elephant in the market. The men had no idea what an elephant was. And even though they could not see, they decided to go to the market anyway. Their goal was to gain an understanding of this wonder they had heard about, if only through touching it. The group went to the market square where each of them touched the elephant.
"The elephant is as a pillar," said the first man, who touched a leg.
"No, it is like a rope," said the second man, who touched the tail.
"Oh no, it is like a thick branch of a tree," said the third man as he touched the trunk of the elephant.
"It is like a big fan," said the fourth man who touched the ear.
"It is like a huge wall," said the fifth man who touched the belly of the elephant.
"It is like a spear," said the sixth man who touched the tusk of the elephant.
They began to argue about the “truth” of the elephant, each of them insisting that he was right. After a while, they became angry with each other. A wise man was passing by and saw their distress. "What is the matter?" he asked them. They said, "We cannot agree what the elephant is like." Each man then described what he thought the elephant was. The wise man calmly explained to them, "All of you are right. The reason every one of you is telling it differently is because each of you touched a different part of the elephant. The elephant has all of those features you described."
"Oh!" the men said, happy that they were each right and content in their understanding of the entire beast.
Teams, whatever their purpose, are usually cross-functional. This means they include “subject matter experts” from several areas of the process being studied—such as stamping, fixture operator, welder and inspector. Just as likely, they are drawn from different disciplines within the business, such as finance, maintenance, operations, quality and engineering. Similar to how the blind men only had knowledge of the part of the elephant they had touched, the information and expertise held by each member of the team is often compartmentalized. Consequently, their thinking regarding root causes, countermeasures, and/or improvements, can only draw from their personal experience of the process, or those parts they have “touched.”
Mapping is the tool that enables us to take each part of the process as experienced and fit them together. By sharing these bits of information (in a systematic approach), and using them to populate a true picture of the process, we get an image that is more accurate. Additionally, each team member becomes more knowledgeable about the process itself. They begin to see how their “piece” fits in with those of their teammates.
This understanding of the whole leads to enhanced performance of the team through an understanding of the internal and external “customers” in the process. It also results in greater improvements, as all the members can bring a larger understanding to bear on the problem or process. It is through Process Mapping that we are allowed to finally see ALL of the elephant. Then we just have to figure out which bite to eat first.
But that is another story…
MEET OUR EXPERT
Chuck Werner, Lean Program Manager and Six Sigma Master Black Belt
Chuck Werner has 27 years of experience in manufacturing, most of it as a Tier I automotive supplier. He achieved his certification as a Lean Six Sigma Black Belt in 1996 and his Master Black Belt certification in 2011. Additionally, Chuck is a certified ISO/QS9000 Lead Assessor, Training Within Industry (TWI) Master Trainer and is certified in OSHA Compliance and Accident Reduction. To read his full bio, click here.
Since 1991, the Michigan Manufacturing Technology Center has assisted Michigan’s small and medium-sized businesses to successfully compete and grow. Through personalized services designed to meet the needs of clients, we develop more effective business leaders, drive product and process innovation, promote company-wide operational excellence and foster creative strategies for business growth and greater profitability. Find us at click here.
Categories: Continuous Improvement,
Lean Principles,
Six Sigma