4/15/2022
BY: SHAUN LEAHEY
Nearly every Quality Manager or Plant Manager has had this situation come up: The phone is ringing and it’s the customer. You instantly get a sinking feeling in your stomach, thinking, here comes a complaint. On the rare occasion there isn’t a problem, you take advantage of strengthening your relationship with the person on the other end of the conversation. But often, you’ll begin the conversation listening to what problem the customer is experiencing and how you can help. Your new priority is to begin problem solving, starting with assembling a team. Wait, we’re supposed to use a problem-solving team? Who’s on the team?
SYMPTOMS OF POOR PROBLEM SOLVING
Symptoms of poor problem solving frequently come from two observations: There is no team, and one person is responsible for the full activity. Or in the lucky event that a team is used, they don’t include the right members on the team. Your efforts are well intended, and you may end up having great problem solvers on the team, but perhaps not with the right experience for the problem at hand. Often, the people who are responsible for leading problem-solving events are not the individuals who have the most knowledge of the process or problem area. Instead, they are individuals who are well voiced at problem solving.
Conversely, process experts such as operators, technicians, material handlers and process owners (people who live and breathe the process, materials and equipment every day), know the details that others don’t but are not included on the problem-solving team. They are talented enough to operate million-dollar pieces of equipment and their insight is invaluable, yet they are not included in the team. This is both interesting and troubling.
UTILIZE YOUR TALENT
Recently, a client of the Michigan Manufacturing Technology Center (The Center) had a quick win during a problem-solving activity. A shutdown event allowed our client to get more people involved in their problem-solving activities, specifically their operators. A brief mention of getting them involved to problem solve led to the question, “Are the operators typically engaged in problem solving?” That question is often asked to confirm an assumption in negativity, while quietly hoping that you get a “yes” or at the very least “sometimes.” It didn’t take long for the lightbulb to go off. When including their process experts in problem solving, the team achieved better results by not only helping determine the root cause and corrective actions, but also by being engaged in the process. Too often, these valuable team members get told what is changing and are instructed to quickly execute the changes rather than have a seat at the problem-solving table.
The reasons team members are not included may be endless. Lack of problem-solving skills may be one of them. Often, there is a propensity to prioritize today’s production over yesterday’s problems (and maybe tomorrow’s sales). As leaders, we have a responsibility to utilize our talent in the best way possible. While it may seem like a difficult decision, engaging talent that has their hands directly on the process that needs repair will bring you much greater return than the short-term constraint you may experience.
CREATING YOUR TEAM
There is no magic number for the appropriate quantity of members of the problem-solving team. Some team members may only be used for a short period of time, while a core team may take a deeper dive. The ability to see things from multiple sides, and from different perspectives, is essential to achieve a robust solution.
The 8D process is one method that can be used for problem solving. And while there are other methods and tools that can result in successfully putting a problem to bed, nearly every method requires you to form a team (it’s the first step in the 8D process). The composition of your team needs to be appropriate for the problem you are solving. It does in fact need to be a team – as in more than one person. By engaging operators, your team may learn more about the process; the things that are non-negotiable, the things that give them problems, the ways they have tried to make things work when adverse conditions present themselves. If nothing else, they will feel like a part of the process. They become invested in the process, and the change, rather than being told to do something new or (maybe worse) how they were part of the problem to begin with.
In manufacturing, the most frequently used team members come from the following areas:
-
Production (operators, technicians, material handlers, etc.)
-
Quality (inspectors, auditors)
-
Maintenance
-
Project/Program Management
-
Suppliers & Vendors
-
Customers
-
Leadership, Management, Supervisors
The idea of problem solving is generally rooted in negativity – you must fix something that’s broken. Make a conscious effort to change the perspective and look at problems as opportunities to improve, engage and develop an environment of solutions. You may even build a team that is great at problem solving, while developing your team's individual skills as well. Not only will they benefit from being part of the process, but they are now further ahead in their own development. Win for problem solving, win for employee engagement, win for leadership and win for personal development.
PROBLEM SOLVING AT THE CENTER
The Center offers several courses to help your company improve its problem-solving skills. Register for an upcoming class
here. Learn more about our Quality Management courses
here.
MEET THE EXPERT: Shaun Leahey, Quality Program Manager
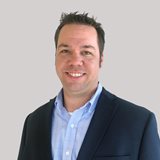
Shaun Leahey is a Quality Program Manager at The Center. Drawing from more than 17 years of experience as a quality professional, Shaun helps Michigan manufacturers achieve business goals, reduce/eliminate defects and elevate customer satisfaction through the application of quality principles. Shaun’s experience with training and developing team members’ quality skills, combined with his expertise in supplier quality assurance, root cause corrective action and Quality Management Systems, enable him to support manufacturers in meeting their Quality objectives.
Since 1991, the Michigan Manufacturing Technology Center has assisted Michigan’s small and medium-sized businesses to successfully compete and grow. Through personalized services designed to meet the needs of clients, we develop more effective business leaders, drive product and process innovation, promote company-wide operational excellence and foster creative strategies for business growth and greater profitability. Find us at www.the-center.org.
Categories: Leadership/Culture,
Quality Management,
The Center,
workforce,
Workplace