10/21/2022
BY: STEVE VAMPLEW
One of the many services we provide at the Michigan Manufacturing Technology Center (The Center) is conducting internal audits on our client’s Quality Management System (QMS) or Environmental Management System (EMS). In today’s manufacturing climate, where labor shortages abound, we are being called upon more than ever to perform these internal audits.
Within the standards of ISO 9001:2015 and IATF 16949:2016, there is a very basic requirement to document a company’s quality policy. This requirement states for, “Top management to establish, implement and maintain” it - which is usually done without any problem.
However, when auditing and interviewing team members to verify that the policy is being “communicated, understood and applied within the organization” (sub-clause 5.2.2), I receive a deer in the headlights look from many team members. Often, they are either completely unaware that a policy exists, do not know where it can be found, or cannot verbalize what it includes or how it relates to their work function.
Now, I’ve never written a major nonconformance for this failure to meet this ISO 9001 requirement – nor does it indicate a total collapse of the client’s QMS. But, I do feel that many owners or top managers take this requirement too lightly and, because of this, do a disservice to their team members.
COMMUNICATION IS KEY WITHIN A SUCCESSFUL BUSINESS
Top management is responsible for ensuring important information gets to the frontline staff to guarantee they are following proper requirements and processes. Informing your employees of important policies will help them feel prepared so that they can perform their job to the best of their ability. There are several ways to fulfill the 5.2.2 clause requirement, such as:
-
Reviewing the policy with new team members during the onboarding process
-
Posting signs of the quality policy throughout the facility
-
Printing the quality policy on the back of employee security badges
-
Using it as the company’s desktop computer screensaver
-
Periodic “spot checks” of team members with rewards for correct responses
-
Top management stressing the importance of their QMS and policy at meetings
Regardless of the way a client ensures this requirement is being met, the quality policy needs to be an important part of their QMS since it sets the foundation for how it does business. It’s top management’s responsibility to train their team members on it, otherwise it will be “open season” for QMS auditors.
The Center’s experienced quality consulting managers have created detailed training and mentoring services to help manufacturing organizations develop an improved QMS. Interested in implementing a QMS or conducting an internal audit?
Contact us today. You can also invest in your staff by registering them for a quality class. Find upcoming courses
here.
MEET OUR EXPERT: Steve Vamplew, Quality Program Manager
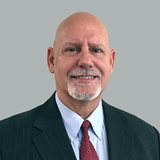
Steve is a Quality Program Manager at the Michigan Manufacturing Technology Center. In his role, Steve manages and delivers consulting, training and implementation assistance for Quality and Environmental Management Systems to small and medium-sized manufacturers. Steve has extensive quality, manufacturing and management experience working in the automotive industry at OEMs and Tier 1 suppliers. He leverages this experience to assist manufacturers with the implementation of ISO 9000:2015, IATF 16949, ISO 14001, AS 9100D and training on automotive Core Tools.
Since 1991, the Michigan Manufacturing Technology Center has assisted Michigan’s small and medium-sized businesses to successfully compete and grow. Through personalized services designed to meet the needs of clients, we develop more effective business leaders, drive product and process innovation, promote company-wide operational excellence and foster creative strategies for business growth and greater profitability. Find us at www.the-center.org.
Categories: Continuous Improvement,
Leadership/Culture,
Quality Management