7/7/2023
BY: CHUCK WERNER
As technology continues to advance, one of our top priorities at the Michigan Manufacturing Technology Center (The Center) is to support manufacturers through their selection of business information systems. From our analysis of more than 500 technology opportunity assessments around the state, we have found roughly 80% of participants have an information system and nearly 90% of those strongly dislike the system they have.
Our clients’ experience when looking for (or struggling with) information systems is a result of at least one of the three root causes below.
Not understanding what the business needs from an information system: If a company doesn’t have a good idea of what they will be using the system for and how it integrates with other systems they may need (or even what their business model is), they are likely to purchase software requiring a great deal of modification (and cost) to get it to where they need it to be.
Blindly talking to a sales representative: Like the point above, talking to a sales rep without knowing what you need the software for can result in purchasing the wrong system. It is important to remember it is the job of the salesperson to sell their product. It is easy to get wrapped up in the product pitch rather than asking the right questions to see if the system is the correct fit for your business.
Shopping fatigue: It typically takes a few meetings before the representatives for an information system want to talk about your business rather than their product. If you start with a handful of potential systems, this means you will have a minimum of 10 meetings (usually 1-2 hours in duration) before you start getting into the details of how the system will work for your business. This can cause a company or individual investigating to make decisions based on the cessation of meetings rather than the support of the software. Fortunately, this is changing throughout the industry. Many system providers realize the premise of “fail fast/fail cheap” applies to whether they are fit with a potential client and is a best practice when implemented on the front end of the engagement. On a side note, if the software you are looking at doesn’t open with a “let’s talk about you” attitude… run (or call us).
While we may soon be able to scratch shopping fatigue from the list, it appears a new issue may be emerging. Nonstandard terminology regarding information systems can confuse the software selection process. Does it function as a document control software, metrics and dashboarding, a manufacturing execution system, machine monitoring, scheduling, manufacturing resource planning, or an enterprise resource planning system? The trick is not in what the system calls itself, but rather in the functionality of the software. Let’s discuss a few performance “buckets” that these offerings fall into.
ENTERPRISE RESOURCE PLANNING
An Enterprise Resource Planning (ERP) system is designed to manage all aspects of an organization's operations. It generally focuses on the strategic or “carpet side” of the business (Level 4 in the image below). In the context of manufacturing, ERP software provides a centralized view of all manufacturing processes, including planning, scheduling, inventory management, production control and quality control.
ERP systems integrate most, if not all, these processes into a single database, providing real-time data on production and inventory levels and enabling manufacturers to make better decisions.
MANUFACTURING EXECUTION SYSTEMS
Next, we have Manufacturing Execution Systems (MES). These software systems are used to monitor and manage the manufacturing processes (Level 3). MES collect and store data on the production process, including the status of the production line, material usage, performance metrics and product quality. This data is used to track the progress of production, identify potential bottlenecks, and optimize production flow. MES provide real-time data on production, enabling manufacturers to respond quickly to changes in demand, identify quality issues, improve production efficiency, and ensure customer satisfaction.
MATERIAL REQUIREMENTS PLANNING
Lastly, there is Material Requirements Planning (MRP) functionality. This software is used to manage the planning and scheduling of materials required for production. MRP considers the quantity of finished products needed and calculates the materials required to produce them. It also considers the inventory levels of raw materials and finished products and creates a plan for purchasing or manufacturing the required materials. MRP systems are designed to help manufacturers optimize their material inventory levels, reduce waste and increase efficiency. MRP functionality is often a part of an ERP for larger companies. It also can be found in some MES systems for smaller ones (overlapping Level 4 and Level 3).
Supporting these three main systems are a variety of more specific software, such as document control, which is used to deliver information to and from associates, collect information regarding the product or process, provide traceability of materials, or just make certain everyone is looking at the latest information. Other popular technologies are those that collect the true run time of equipment and allows the associates to add contextualization to run time, scrap rates, process delays, etc.
As with all technology implementations, it is important to understand what problem you are trying to solve. Perhaps the only thing a company needs to know is how much their equipment is running and the reasons it isn’t. Some companies may need to know where their “stuff” is while other companies may need shop floor visibility. Finally, some may need all the above. Education and some level of long-term strategy are essential to properly ensure a plan of growth and to make certain that each information system can communicate up to the next level or develop on the shop floor.
IMPLEMENTING A SYSTEM WITH THE CENTER
The Center’s experts are here to help your business adopt the best system to reach your goals. Our team will complete a
free technology opportunity assessment to identify where technology can be best applied to your company. We are here to support you every step of the way from choosing a system to implementation and beyond.
Contact us today to get started.
MEET OUR EXPERT: Chuck Werner, Manager Operational Excellence/Lean Six Sigma Black Belt
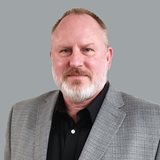
Chuck has been a member of the team at The Center since 2016. His areas of expertise include Lean, Six Sigma and Quality. Chuck has devoted many years to practicing Six Sigma methods, ultimately earning a Six Sigma Master Black Belt in 2011. He is passionate about helping small and medium-sized manufacturers become more prosperous using a variety of tools and methods gathered from over 30 years of experience in manufacturing.
Since 1991, the Michigan Manufacturing Technology Center has assisted Michigan’s small and medium-sized businesses to successfully compete and grow. Through personalized services designed to meet the needs of clients, we develop more effective business leaders, drive product and process innovation, promote company-wide operational excellence and foster creative strategies for business growth and greater profitability. Find us at www.the-center.org.
Categories: Advanced Manufacturing,
Continuous Improvement,
Data & Trends,
Industry 4.0