7/14/2017
BY: DAVID BRADLEY
ISO 9001:2015 blends documents and records into a single concept called “Documented Information” and no longer requires any documented procedures. If you’re still in the ISO transition phase, you might be thinking that certain procedures for handling documents and records got a lot more complicated—but did they?
If your procedures for documents and records served you well under the 2008 version, they will probably do the same for the 2015 version. Just because they are no longer mandated does not mean they should be discarded. (This holds true for any document or record you had under the 2008 version.) So, how can you tell if you can discard any of your old documents or if you need additional documentation you did not have in the past?
To help prevent paperwork overload, ask yourself the following questions:
- Is the document required by the standard? If the standard requires you to have documented information, does this document meet that requirement? If the answer is yes, then you need to keep (or perhaps generate) the document. Or, you may need to modify the document to meet the requirements or intent of the standard. If the answer is no, then proceed to the next question.
- Is the document required by either your customer or governmental (regulatory) entity? If either your customer or the government requires the document, then you need to keep it. As with question one, you may need to modify it to meet the requirements. If neither your customer nor the government mandates the document, then advance to question three.
- Is the document required? You may have documents that are not required by anyone external to the organization, however, the absence of the document could result in unwanted variation. Think of pain here. If we remove the document, could you experience pain? There also may be pain because of the document. Perhaps the document prohibits the flexibility required to effectively and efficiently engage the process. If it is required by necessity, then you must keep the document. Again, modification may be necessary for the document to meet your operational needs. If it is not required by necessity, then jump to the final question.
- Is it desirable to keep the document? While some documents are not required, they still might be worthwhile to keep.
By asking these questions, you can quickly identify documents that will remain part of your Quality Management System and those that can be discarded. When tossing documents, it’s often helpful to keep a copy in archive.
In any instance, your documents should be up to date with the requirements and your processes.
As processes are performed, verify the documents are still the appropriate reflection of the current practice. As you engage your customers, verify any change to customer requirements. Also, many regulatory documents are reviewed or revised on a yearly basis. Keep track of those changes as well.
Your documentation should assist you in providing a quality product or service. Remember, a well-run system will work for you, not the other way around. Use common sense and frequently ask yourself the previous questions to help maintain a successful Quality Management System that keeps documentation at a minimum level—and your head above water.
MEET OUR EXPERT
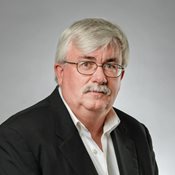
David Bradley, Quality and Environmental Services Program Manager
David Bradley has been The Center’s Program Manager in QMS for 18 years and is a member of the Quality Team. His expertise includes ISO 9001, TS 16949, AS 9100, ISO 13485 management systems, Automotive Core Tools, ISO 14001 Environmental Management Systems and OHSAS 18001 programs. To read David’s full bio, click here.
Since 1991, the Michigan Manufacturing Technology Center has assisted Michigan’s small and medium-sized businesses to successfully compete and grow. Through personalized services designed to meet the needs of clients, we develop more effective business leaders, drive product and process innovation, promote company-wide operational excellence and foster creative strategies for business growth and greater profitability. Find us at www.the-center.org.
Categories: Quality Management