2/15/2019
BY: RON QUINKERT
As we discussed in a recent blog, many manufacturers are
deciding now is the time to diversify. With a potential recession on the horizon, organizations are faced with a few different diversification options to pursue: develop new types of products, sell to new geographic areas or expand into new industries.
But before companies can commit to expanding into new markets, for example, they must first answer a few important questions, such as: Which industries will provide the most business opportunities, now and in the near future? How do I successfully enter a new market? Which industry would make the most sense for my business to enter into?
One industry that has experienced steady growth in recent years is the aerospace sector. With commercial aircraft demand skyrocketing due to factors such as stable crude oil prices, growth in passenger travel and global tensions contributing to higher defense spending, the aerospace industry has become one of the most viable markets for manufacturers to operate in. Due to its promising revenue streams now and in the coming years, many manufacturers might decide that entering the aerospace sector is the right decision for their business. But how do organizations go about doing this?
When it comes to aerospace, quality is the number one priority. After all, it is rare that we hear of airplane recalls or disasters due to manufacturing errors. Because of this, any manufacturer who aims to find success in the aerospace industry must start by achieving an AS9100D certification.
First released in 1999, with the most recent revision published in 2016, AS9100D Quality Management Systems – Requirements for Aviation, Space and Defense Organizations is the standardized Quality Management System (QMS) for the aerospace sector, as well as for defense organizations. Essentially, AS9100D encompasses all the requirements outlined in the more general ISO 9001 quality standard, with additional requirements specifically related to aviation, space and defense organizations.
In addition to ensuring all manufactured parts reach specified standards of quality, having a QMS that is registered to AS9100D can improve manufacturers’ delivery performance while reducing production costs. Maintaining this certification also helps drive continuous improvement initiatives, as manufacturers must continually work to improve processes and prioritize quality in order to keep their AS9100D certification.
Unlike the domestic automotive industry’s requirement to another QMS standard, AS9100D certification is not mandatory for manufacturers to obtain. However, many aerospace customers still require suppliers to achieve a certification in order to conduct business with them. Because of this, manufacturers who choose to get this certification can gain a competitive advantage over others who have not.
Manufacturers with more questions about the process, costs and responsibilities associated with entering the aerospace sector can get answers at an upcoming Aerospace Industry Association of Michigan (AIAM) event. Hosted by The Center at our Plymouth location, this lunch and learn event will be held from 11am to 2pm on Tuesday, March 19. Speakers from the industry will share insights about what manufacturers must do in order to successfully enter the aerospace industry, and why they would want to. To register for this event, click here. Companies do not have to be an AIAM member to attend.
MEET OUR EXPERT
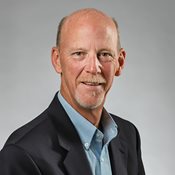
Ron Quinkert, Senior Business Solutions Manager
Ron Quinkert is a Senior Business Solutions Manager with the Michigan Manufacturing Technology Center and has 20 years of automotive sales and manufacturing experience. He works directly with manufacturers in seven Southeast and Central Michigan counties. Ron is a seasoned professional with expertise in team building, automotive product and manufacturing processes, tool design, operational audit practices, procedures and improvements.
Since 1991, the Michigan Manufacturing Technology Center has assisted Michigan’s small and medium-sized businesses to successfully compete and grow. Through personalized services designed to meet the needs of clients, we develop more effective business leaders, drive product and process innovation, promote company-wide operational excellence and foster creative strategies for business growth and greater profitability. Find us at www.the-center.org.
Categories: Growth,
Quality Management