2/10/2017
BY: ANDY NICHOLS
Ch-ch-changes...
The 1974 David Bowie song suggests the singer has to
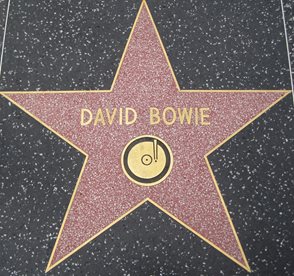
“turn and face the strange,” and at first sight, some of the new requirements for ISO 9001:2015 might look like a
“Space Oddity.” There’s the addition of “risk,” nothing about any documented procedures, quality manual or even that the role of the “management representative” is missing. And, what about the new layout? The so-called “Annex SL” structure expands the requirements, numbering from 4 through 8 to 4 through 10? Definitely strange for some! With the clock already started to tick away on the deadline for the upgrade, is your organization now
“Under Pressure”?
If you use your current ISO 9001:2008 Quality Management System, you have all the tools at your fingertips to plan and implement the revisions:
Quality management system planning – 5.4.2
“Top management shall ensure that The planning of the quality management system is carried out in order to meet the requirements given in 4.1…and,”
“the integrity of the quality management system is maintained when changes to the quality management system are planned and implemented”
Management Representative – 5.5.2
“a) ensuring that processes needed for the quality management system are established, implemented and maintained…”
Management review – 5.6.1 General
“This review shall include assessing…the need for changes to the quality management system…”
Review input 5.6.2
“The input to management review shall include information on
f) changes that could affect the quality management system”
There is, however, a challenge for implementation in that organizations simply don’t go home on Friday, after switching off their 2008 QMS, and arrive the following Monday to a new, 2015-based way of managing Quality. ISO 9001 also indicates what has to be considered in the transition:
Quality management system – 4
“The organization shall establish, document, implement and maintain a quality management system…in accordance with the requirements of this International Standard”
“These processes shall be managed by the organization in accordance with the requirements of this International Standard”
A key part of planning is going to be the use of the organization’s “Management Review.” If the organization adopts “P, D, C, A” as its methodology, the review becomes a platform for management of change, instead of just being something “ISO” requires.
WARNING: An organization which carries out their Management Review or Internal Audits once per year may wish to consider that, when set against the available transition 18 month window and the P, D, C, A cycle, more frequent internal audits and reviews will be needed to maintain control and assure a successful recertification!
If we take, as an example, the dropping of the requirement for a Quality Manual – and put it as an input to Management Review – management would need to:
a) Consider the effect of no longer having a Quality Manual
• On the organization
• On customers’ needs and expectations
• On regulatory compliance
b) Consider the value of a Quality Manual to the organization
• As a means of communicating quality policy, quality objectives, the scope of the
management system, exclusions and any justifications, etc.
• Describing the sequence(s) and interaction(s) of the processes of the quality management
system
Having reviewed this, the ISO 9001:2008 requirements then go on to indicate what should happen:
Review output 5.6.3
“The output from the management review shall include any decisions and actions relating to
a) Improvement of the effectiveness of the quality management system and its processes…
c) Resource needs”
It may well be that management decides to keep the quality manual as “documented information” (another requirement which has changed terminology) in light of perceived customer needs and expectations. A further decision may be to improve the format of the existing quality manual so it doesn’t simply follow the ISO 9001 layout, since no-one in the organization reads/understands it! Of course, in deciding to do that, someone will be assigned to the tasks associated with those decisions.
You’re Not “Absolute Beginners”
We’re nearly halfway through the three-year transition period given to organizations to revise and recertify their Quality Management Systems to the ISO 9001:2015 requirements. Engage the various requirements of your current Quality Management System, and by using them as they were intended, you’ll see a big benefit. Unconvinced? Call 888.414.6682 and speak to one of our experts here at The Center.
The next 18 months may prove a golden opportunity to make much needed improvements, and you could be “Dancing in the Street” after your ISO upgrade audit!
MEET OUR EXPERT
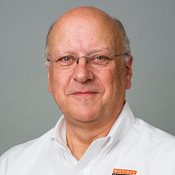
Andy Nichols, Quality Program Manager
Andy has 40 years of expertise in a wide variety of roles and industries, with a focus on quality management systems in manufacturing organizations. In addition to his ISO 9000 Management Systems experience, he has worked extensively with ISO/TS16949, ISO/IEC 17024 and ISO/IEC 17025.
His broad practical knowledge of ‘Quality Tools’ includes: SPC, FMEA, Quality Circles, Problem Solving, Internal Auditing and Process Mapping. He also has been an IRCA and RABQSA accredited Lead Auditor. To read Andy's full bio, visit www.the-center.org.
Since 1991, the Michigan Manufacturing Technology Center has assisted Michigan’s small and medium-sized businesses to successfully compete and grow. Through personalized services designed to meet the needs of clients, we develop more effective business leaders, drive product and process innovation, promote company-wide operational excellence and foster creative strategies for business growth and greater profitability. Find us at www.the-center.org.
Categories: Quality Management