12/16/2022
BY: MATT SHOFFNER
While touring a facility, I always look at how workspaces are organized. Occasionally, I see evidence of past Lean initiatives. 5S is the easiest Lean tool to spot on a tour and it is also the easiest to identify when it is no longer in use. When I find 5S that is no longer being followed, I call it a 5S graveyard because that is where 5S went to die. 5S graveyards were once initiatives optimized to improve flow through visual management of a workplace for inventory, tools and everything needed to do a specific job.
The 5S graveyard reveals which Lean principles have been lost, misunderstood, forgotten and/or ignored. Have you ever noticed a broom leaning against a wall next to a shadow board that clearly indicates where the broom should hang? Have you opened a tool chest with foam cutouts to indicate where tools should rest, and the tools are scattered on top of the foam? These graveyards illustrate the time someone invested to organize an area that was later ignored.
When we do a postmortem on a broken 5S system, the most common causes of death include:
-
If 5S is pushed on a team without buy-in, it will die.
-
If 5S is not standardized, audited and discussed, it will die due to lack of accountability.
-
If you don’t discuss 5S results regularly, it will be forgotten, and you will find yourself with a graveyard soon after.
-
If management does not reinforce the importance of 5S it will fail. If it isn’t important to you, why would anyone else care about it? Posting stats on which areas are passing or failing their audits is a powerful reinforcement for teams to sustain 5S in their area.
The key to 5S success relies on leaders securing buy-in from the team and creating an accountability system for sustainability. As a leader, the quickest way to destroy 5S is to stop doing your part. If you neglect to address items in the red tag area or let poor 5S adoption persist, then you are letting your 5S system deteriorate. If this continues, your tombstone will read, “Here lies Lean. We tried, sort of.”
The good news is that a 5S system can successfully be revived. The gains from implementing Lean systems far exceed the costs - regardless of how many times you try. Revitalization takes effort. You will need to convince the team that this time the system will be sustained. Put in the time to make it work for the long run!
The Michigan Manufacturing Technology Center is here to help you bring your 5S program back to life.
Contact us to avoid a graveyard! Want to learn more about our Lean services? Click
here.
MEET OUR EXPERT: Matt Shoffner, Senior Business Solutions Manager
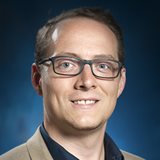
Matt Shoffner is the Senior Business Solutions Manager for the Michigan Manufacturing Technology Center Northeast Regional Office at Saginaw Valley State University. Shoffner is responsible for improving the competitiveness of small and mid-sized manufacturers in the State of Michigan. He does this by diagnosing problems and then prescribing solutions that result in sales growth, greater efficiencies, and employee engagement. He specializes in culture change, operational effectiveness (Lean), problem solving, and strategic planning.
Since 1991, the Michigan Manufacturing Technology Center has assisted Michigan’s small and medium-sized businesses to successfully compete and grow. Through personalized services designed to meet the needs of clients, we develop more effective business leaders, drive product and process innovation, promote company-wide operational excellence and foster creative strategies for business growth and greater profitability. Find us at www.the-center.org.
Categories: Continuous Improvement,
Lean Principles,
Manufacturing