4/1/2022
BY: ANDY NICHOLS
At first sight, this may seem to be a crazy question. I hear you say, “Seriously? Calibrate Internal Quality Auditors?” or “Where does the calibration sticker go?”
Internal Management System Auditors can be “testing” the Quality Management System (QMS) and could be considered as items of testing equipment. Their brief, in the widest possible terms, is to inspect or evaluate the QMS for compliance and effectiveness.
It might not seem so far-fetched if you consider the following:
-
The ISO 9001 requirement to perform internal audits is found in Section 9 which is entitled “Performance Evaluation.”
-
Internal audits are conducted to provide information about the Quality Management System – and that’s got to be accurate, right? Otherwise, why do them?
-
Internal Auditor selection ensures objectivity and impartiality. We can substitute the words “unbiased” for objectivity and “neutrality” for impartiality. While Internal Auditors are engaged in the role, how do we know they remain stable?
-
In other words, would a given scenario result in a similar finding etc. in six or 12 months? We could ask how stable the Internal Auditor’s response to a given situation is. Shouldn’t it be similar, if not the same?
For those readers who have inhabited the world of Metrology, you’ll be familiar with the terminology associated with calibrating (or verifying) test equipment, and three types of studies performed, so we may better understand the impacts the equipment has on testing results. Those studies are bias, linearity and stability.
Like the initial calibration of an item of equipment, the initial training of Internal Management System Auditors is the first step. To quote an old trope, “training makes people dangerous.” It would be dangerous if we continued to test products with an item of test equipment which wasn’t periodically checked to ensure it is giving accurate results. Yet, this is exactly what happens with Internal auditors. Once initial training is given, what happens after that? No one considers that aspect…
Traditionally, the only time that Internal Management Systems Auditors are considered as needing training is when the ISO standard changes. Until 2021 it was approximately five years between each revision of ISO 9001, so at least there was an opportunity to recheck what the auditor was doing (or was there?). Even by conservative estimates, five years is a long time to let an item of measuring equipment go unchecked. In 2021, the ISO T/C 176 decided not to amend the standard for another few years! Waiting even longer to refresh an Internal Auditor’s skills? Doesn’t sound good, does it?
A Google search for ISO 9001 Internal Auditor training reveals more than 3 million results – for that initial training course, however, if the search is modified to include the keywords “refresher training,” the population drops to a paltry 55,000 and many results don’t include the keyword “retraining.”
It therefore falls to organizations to ensure the continuing competency of their Internal Management System Auditor(s). Training isn’t a one-time deal. If we consider Broadwell’s model of “4 levels of teaching” it can be understood that these are not concrete. Things change and with those changes, competencies change too.
If your organization is struggling with how to get the most value from the Internal Audit Process, it might be an auditor retraining issue. Contact us
here to get your auditor recalibration scheduled – we’ll even supply a calibration sticker!
For assistance with your company’s Quality Management Audits, The Center’s experts can help. Search upcoming Quality Management classes or contact inquiry@the-center.org for more information.
MEET OUR EXPERT: Andy Nichols, Program Manager
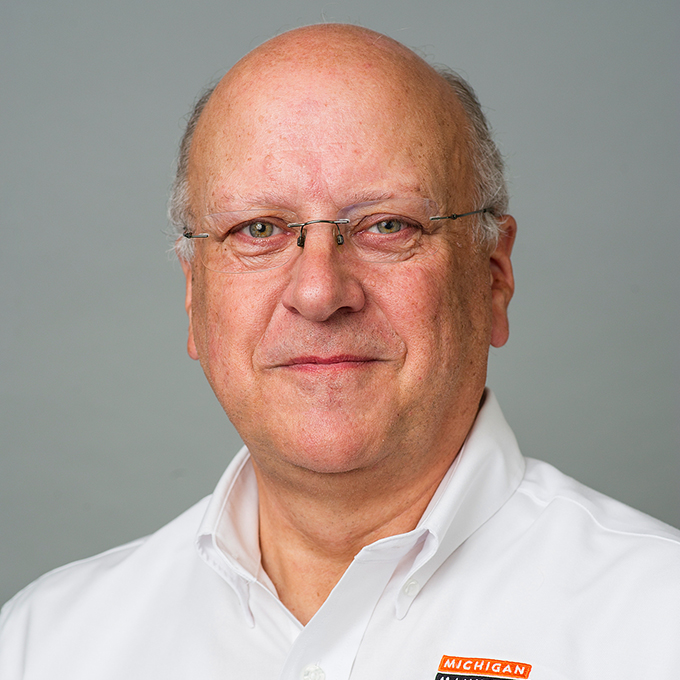
To The Center’s clients, Andy Nichols, CQP MCQI, brings 40 years of expertise in a wide variety of roles and industries, with a particular focus on quality management systems in manufacturing organizations. Prior to joining the Michigan Manufacturing Technology Center, he was the East Coast Regional Sales Manager for NQA, a “Top 5” Global Certification Body, responsible for significant sales growth in a highly competitive marketplace. He has authored two books, “Exploding the Myths Surrounding ISO 9000 – A Practical Implementation Guide” (published by ITG in April 2013) and “A Guide to Effective Internal Management Systems Audits" (published May 2014).
Since 1991, the Michigan Manufacturing Technology Center has assisted Michigan’s small and medium-sized businesses to successfully compete and grow. Through personalized services designed to meet the needs of clients, we develop more effective business leaders, drive product and process innovation, promote company-wide operational excellence and foster creative strategies for business growth and greater profitability. Find us at www.the-center.org.
Categories: Quality Management