4/22/2022
BY: ANTHONY WELSH
We have now discussed the idea of
creating a data-driven culture of thinking by using the mathematical formula Y=f(x) + N. Last time we focused on the Y. Remember,
the Y is important to get correct first, so be sure to go back and read this article if you haven’t.
Continuing this series, let's begin investigating the right side of the equation. An X is an input, also known as an independent variable, or a factor we can manipulate. Some examples include a dial or setting on the machine, a material property, this profile vs. that profile, the proportions of ingredients, etc. In the equation Y=f(x) + N, X is distinguished from N because it’s controllable where N is something we can’t control. We’ll cover noises in the next article.
LEARNING ABOUT THE FACTORS
This is a fantastic part of the project where we begin to gain knowledge about the factors. We quickly determine which ones make a real difference in the output and which ones do not. You start to feel like you have some level of control as you discover ‘knobs’ that you can turn, where previously it was a mystery why things were changing. You’ll then start to determine how you should set those knobs to achieve the desired output.
This makes the basic Y=f(x) equation expand to Y=f(x1, x2, x3, x4) as you add in the active factors that matter. The excitement builds as you ask new questions and test theories in a sequential manner sorting out the active effects from the things that don’t matter. It’s critical to run these experiments so you can find those “vital few out of the trivial many” factors that can help us understand the Y=f(x) of our process or product.
For a more specific example, we demonstrate this concept on a wooden catapult in class. Students are encouraged to explore things like rubber band type, ball type, various pin and pull back settings on the catapult, the effects of operator and their launching style, the measurement system, etc. Each team finds the Y=f(x) of their individual process even though the classic kinematic equations would predict the same answer for every team. The textbook formula doesn’t consider the nuances of each team’s process and thus collecting new data yields a better prediction. A target is then placed on the field and teams get one chance to make their prediction, setup the catapult and hit the target.
USING SIX SIGMA TO FIND SOLUTIONS
In Six Sigma training we cover how to run the most efficient type of experiment based on the questions you are trying to answer. Consider how we might approach an experiment differently if you have no idea what factors are active versus trying to determine the best level settings for known active factors. These are very different designs. Now, one could try just stabbing in the dark, changing this or that and seeing what happens, but that sounds like a very inefficient strategy. In class we compare various experimental strategies, and you’ll learn the skills needed to design, execute and analyze a proper design based on your project questions. This is the best way to get the required knowledge you need to solve your problems while being limited by finite resources.
When I say experiment, I bet you’re thinking of the old dogma, isolate a single variable which you change and hold everything else constant. But imagine having the ability to vary multiple factors at the same time in one experiment and being able to learn about all of them. This may seem crazy, but yes you can learn about more than one factor at a time and know how each one independently affects the response.
Not only that, but we can also learn about their potential interactions. What is an interaction you ask? This is also fully explained in Six Sigma training. The unfortunate thing is many single variable experiments are performed and they are unable to learn about interactions, yet in nature, interactions are quite common. Think about the simple relationship of time and temperature while cooking or baking. There is an interaction there because the length of time you should cook something depends on the temperature in the oven. You can’t consider time alone or temperature alone.
SO, WHAT’S THE POINT?
The real goal is that by the end of the project you’ve shifted your focus from the Y to the X. If all you’re doing is monitoring the Y, what does that mean when you detect a problem? It means the problem already exists! That’s just too late. We want to be proactive, not reactive. That requires understanding the Y=f(x) of your process or product so that you know the output will be good based on how you set and control the inputs. This is when we can really achieve some level of stability, predictive power and ongoing customer satisfaction.
SIX SIGMA AT THE CENTER
The Center’s courses combine proven problem-solving methods with powerful statistical tools to construct a reliable roadmap to improve business operations. Learn more about the Six Sigma courses we offer
here.
MEET OUR EXPERT:
Anthony Welsh, Six Sigma Master Black Belt
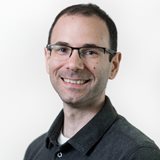
Anthony Welsh is a Six Sigma Master Black Belt with 20 years of experience delivering projects to both the automotive and consumer products industries. In his role at The Center, Anthony shares expert tools in critical thinking and data-driven decision making to assist clients with using Six Sigma methods to achieve real results.
Since 1991, the Michigan Manufacturing Technology Center has assisted Michigan’s small and medium-sized businesses to successfully compete and grow. Through personalized services designed to meet the needs of clients, we develop more effective business leaders, drive product and process innovation, promote company-wide operational excellence and foster creative strategies for business growth and greater profitability. Find us at www.the-center.org.
Categories: Six Sigma