As we all know, technology is advancing by the day, hour and minute, which means so is manufacturing. To assist manufacturers, the Michigan Manufacturing Technology Center (The Center) provides free Technology Opportunity Assessments. During this assessment, The Center’s experts visit a manufacturing site to see where automation and technologies could help ensure the company doesn’t get left behind. So, what have we learned after completing more than 200 of them?
COMMON AREAS TECH CAN HELP
It is essential that manufacturers prepare for and begin implementing Industry 4.0 technologies. Doing so will keep them competitive in the industry and ensure they are staying up to date in the latest improvements. Through our assessments, our experts have noticed specific areas technology and automation can benefit companies such as:
GET READY TO ADOPT TECH
As we tour hundreds of different manufacturing facilities, there are common things we see that need to be done before technology is implemented. To successfully implement technology, leadership needs to be committed to the change, the team needs to be on board and processes need to be in place.
At The Center, we use the ISA-95 Technology Adoption Model to show the different levels at which technology can be adopted to help processes work more efficiently. Many companies focus on their ERP (level 4), but this is only part of the manufacturing formula.
WALK THROUGH THE TECHNOLOGY ADOPTION MODEL 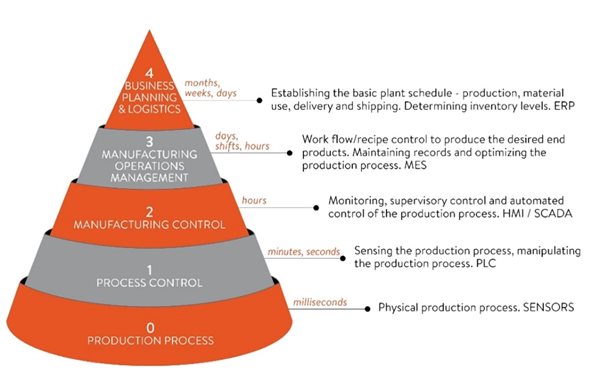
A great example is a high-volume, low-mix environment where it is critical to understand if the equipment is running (and making parts). When operators stop production to look for material, tools, supervisor support or equipment failure, they move from direct to indirect labor. When equipment has appropriate sensors (levels 0 and 1), supervisors have instant access to those operators that aren’t running to schedule. For those in a low-volume, high-mix, or prototype environment, understanding where variances occur and the how delays can impact operations later in the process is critical to improve schedule compliance and employee morale.
In level 2, SCADA (supervisory control and data acquisition) connects sensors that monitor equipment like motors, gears, pumps and valves. This allows supervisors to access information on equipment use and performance. Prior to the availability of this information, supervisors would walk the aisles to see equipment status and intervene when they noticed a problem. For larger facilities (or where equipment is in an indirect vantage point from the supervisors’ office), this becomes a greater operational challenge and causes more indirect labor to be wasted.
In level 3, a dynamic schedule can measure how long those downtimes last, the impact on the production schedule and on-time delivery. Also, by keeping track of reason codes and the cost of downtime, managers can better understand the impacts on the business. They can discuss, with supporting data, where to invest in equipment upgrades and employee training and identify where the greatest return would occur when investing capital.
START THE PROCESS WITH HELP FROM THE CENTER
When The Center performs Technology Opportunity Assessments, several questions are asked pertaining to the example I just provided. The usual pressing question is what your minimum gross margin and what is your actual gross margin. Many times, the delta (difference) is more than 5%. For a $10 million company, that means there is approximately $500,000 of profit that isn’t realized. Once we identify this, we can create a customized strategy for your company to adopt technology where it is most needed.
Our experts at The Center are here to help you throughout the whole journey. Once we perform a Technology Opportunity Assessment, we will establish an adoption strategy, scope the project, align suppliers with vetted resources and manage implementations to ensure business and customer needs are met.
SCHEDULE YOUR ASSESSMENT TODAY
Stay ahead of the game and get started with Industry 4.0.
Schedule your free assessment here. Manufacturers are encouraged to start training their team with our innovative classes that will assist them in better understanding Industry 4.0 before, during and after implementation. See upcoming courses
here.
MEET OUR EXPERT: George Singos, Industry 4.0 Business Leader Advisor
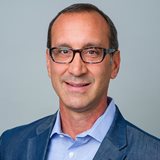
George Singos is the Business Leader Advisor for the Michigan Manufacturing Technology Center (The Center). He has more than 30 years of manufacturing experience in various capacities. For the past 20+ years, he has focused on sales and marketing management both domestically and internationally. Prior to joining The Center, George spent the previous 10 years working in International Business Development. His primary focus was growing International Sales in Europe and East Asia while supporting North American, South American and ASEAN operations.
Since 1991, the Michigan Manufacturing Technology Center has assisted Michigan’s small and medium-sized businesses to successfully compete and grow. Through personalized services designed to meet the needs of clients, we develop more effective business leaders, drive product and process innovation, promote company-wide operational excellence and foster creative strategies for business growth and greater profitability. Find us at www.the-center.org.