9/23/2022
BY: ROGER TOMLINSON
Take a look at your facility. Are there ways you could improve the layout of your plant? Are employees walking far between jobs? Does the arrangement of equipment make the most sense for optimum efficiency?
Plant layout is a great way to minimize operating costs by ensuring efficient workflow throughout the shop floor. It is the most effective physical arrangement of machines, processing equipment and service departments allowing for the greatest coordination of labor, materials, machines and methods within the factory.
WHEN IS PLANT LAYOUT REQUIRED?
A new plant layout is a great way to cut wasted time and labor. It may be required when one of the following occurs.
-
There are design changes in the product
-
There is an expansion of the company
-
There is proposed variation in the volume of products made
-
New products are added to the existing line
-
A new department is added to the company and/or there is reallocation of the existing department
-
A new plant or building is added
IMPORTANT FACTORS TO CONSIDER
To attain the best layout for your facility, a few factors come into play that will affect the flow and efficiency while considering where the right place is for each piece of equipment.
- Weight, volume, or mobility of the product
- If the final product is heavy or difficult to handle, involves costly material handling equipment or a large amount of labor, it’s important to consider moving the product the least number of times possible.
- Complexity of the final product
- If the product is made up of many components and parts, a considerable number of people may be employed for handling the movement of these parts from shop to shop, machine to machine or one assembly point to another.
- Length of the process in relation to handling time
- If the material handling time represents a significant amount of the total time of manufacturing, any time reduction in handling the product may result in great productivity improvement.
- High-volume mass production
- High-volume production output will require more material handling personnel unless the layout is good.
DIFFERENT TYPES OF PLANT LAYOUTS
There are several types of plant layouts that depend on the company’s product and processes. It is important to adapt the layout according to your needs.
Process Layout
These layouts are primarily found in job shops or companies that produce customized, low-volume products that require different processing requirements and sequences of operations. The purpose of this layout is to process goods or provide services that involve a variety of processing requirements.
Product Layout
Product layouts are found in flow shops that produce high-volume, highly standardized products that require repetitive processes. In a product layout, resources are arranged sequentially, based on the routing of the products. A sequential layout allows the entire process to be laid out in a straight line, dedicated to the production of only one product or product version. The flow of the line can then be subdivided so labor and equipment are utilized smoothly throughout the operation.
Fixed-Position Layout
A fixed-position layout is appropriate for a product that is too large or too heavy to move. Services may dictate the fixed position (e.g., a hospital operating room where doctors, nurses and medical equipment are brought to the patient).
Cellular Layout
Cellular manufacturing is a layout where machines are grouped according to the process requirements for a set of comparable items (part families) that require similar processing. Processes are grouped into cells with parts with similar design characteristics (size, shape and function) and similar process characteristics. Workers in cellular layouts are cross trained so they can operate all the equipment within the cell and take responsibility for output.
EIGHT PRINCIPLES OF LEAN PLANT LAYOUT
There are eight principles that serve as a guide to help design a Lean plant layout. When we work with our Michigan manufacturers, these steps allow us to ask questions to find the right places and flow for their facility.
-
Subject all layout decisions to the goals and objectives of the organization and the production system
-
Reduce transfer distance of materials (from dock to dock and from process to process)
-
Reduce throughput time for the entire facility and for individual departments
-
Reduce inventory between processes and within a process
-
Maximize machine density
-
Eliminate barriers to optimal production and material flow
-
Expose and eliminate waste
-
Employ benchmarking plus physical constraints to support the above principles
It is best to start with a “mentally” clean slate and ask, “What would the ideal layout be?” That will give you something to work towards. Layout design will near the ideal completion when it meets most, if not all, of your objectives.
GET LEAN WITH THE CENTER
The Center is here to help you increase efficiency and reduce waste. Plant layout is a great way to do both! Our Lean performance management consulting services will develop a personalized implementation strategy to aid in the improvement of your processes.
Schedule a free assessment and
register for an upcoming lean course to start the journey towards improvement.
MEET OUR EXPERT: Roger Tomlinson, Lean Program Manager
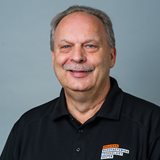
Roger has been a Program Manager in The Center’s Lean Business Solutions program for more than 20 years. He has trained and mentored hundreds of Michigan manufacturers in the entire portfolio of Lean strategies and methods (e.g., Kaizen events, Standardized Work, 5S/Workplace Organization, Value Stream Mapping, Total Productive Maintenance, Culture Change, Team Building, operations management and process re-engineering). In addition to his training and consulting work, Roger has more than 20 years of experience in manufacturing management.
Since 1991, the Michigan Manufacturing Technology Center has assisted Michigan’s small and medium-sized businesses to successfully compete and grow. Through personalized services designed to meet the needs of clients, we develop more effective business leaders, drive product and process innovation, promote company-wide operational excellence and foster creative strategies for business growth and greater profitability. Find us at www.the-center.org.
Categories: Lean Principles,
Manufacturing,
The Center,
Workplace