9/13/2019
BY: ANDY NICHOLS
During the past 15 to 20 years, the use of lean tools from the Toyota Production System has become popular in U.S. manufacturing. This is nearly the same time frame in which ISO 9001 Quality Management Systems and Certifications have been adopted by manufacturing businesses. Oddly, despite the importance of lean tools in determining the effectiveness of processes, it’s rare for Internal Quality Systems Auditors to be trained on these methodologies.
Commonly, internal quality auditors conduct their audit assignments only to make sure everyone is “following procedures.” After all, they’ve heard that ISO compliance means, “Say what you do, do what you say.” Unfortunately, this approach fails to address the effectiveness of only doing what is written down. This neglect results in important facets of any QMS being overlooked.
CONSIDER THE FOLLOWING (REAL LIFE) EXAMPLE
During the internal audit of an assembly line, the first operation (OP 10) is described in the assembly work instructions as: “Locate the motor end plate in the fixture. Align the bearing with the large hole. Press the bearing into the motor end plate.” Observing the hydraulic press operator, the internal auditors confirmed that the instruction was followed, although it took the operator multiple attempts to ensure the bearing was pushed into the end plate fully. The operator then placed the completed end plate on the conveyor.
At the second station (OP 20), there are two operators on one side of the conveyor. They attach the motor end plate loosely to another assembly with four long screws. They then place the loose assembly back on the moving conveyor where a guide directs the product to station three (OP 30) for tightening of the screws. The station three operator uses an electric torque driver to tighten the screws. Once again, the auditors all confirm that the operators are performing the work according to the OP 20 and OP 30 instructions available.
The final operation (OP 40) is testing, where the assembled motor is run on an electrical test bench. Once again, testing is accomplished to the prescribed instructions and any failures are red tagged and set aside for rework - all compliant, the internal auditors confirm.
The auditors then check for document control and confirm the work instructions are the latest versions. All product containers are clearly labeled for the assembly line and the torque driver has a calibration label on it, as does the electrical tester. All is in order. The assembly line has a skills matrix posted which shows all the operators are trained and competent for the operations they perform. Test failures are correctly tagged with a record of the reason(s) for test failure, which is usually “high torque” because the unit was assembled incorrectly, and segregated for rework.
According to the internal auditors, everything is compliant to the documented Quality Management System and, hence, with ISO 9001:2015 requirements. Who wouldn’t agree?
DON’T BE SHALLOW…LOOK PAST THE SURFACE
If the process were observed through the eyes of an individual confident in lean processes, the following issues would have been noted:
- The press needed to be cycled three or more times to ensure the bearing was pushed into the end plate fully
- The assembly line is “unbalanced”
- The process isn’t based on one-piece flow
Reviewing the process from this lean perspective, we can see that OP 10 is causing one of the eight forms of waste (see figure below) – Motion – because the press activity is only “right the first time” one in three times (or worse), so the operator must make multiple attempts to get the bearing into the end plate. The press doesn’t operate correctly due to a maintenance issue, which had been reported several times by the press operator.
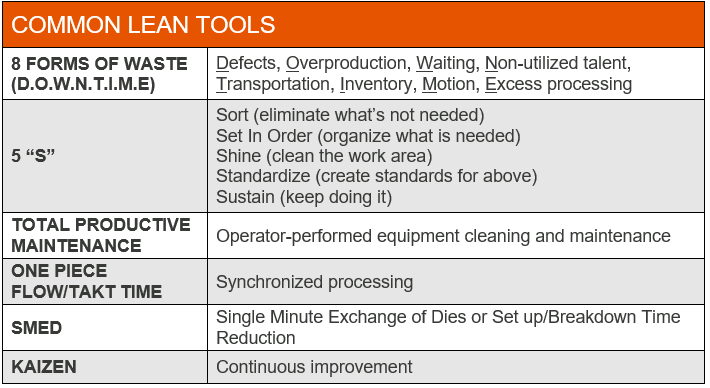
Because there are two operators at OP 20, twice as many products are flowing to the single operator at OP 30. As a result, the operator cannot finish the operation completely and accurately in the time allowed. This results in a failure to meet takt time, or the rate at which a product must be produced in order to meet customer demand.
The final station, OP 40, identifies Defects, another form of waste due to poor production quality.
Had the internal quality auditors viewed the process beyond simple compliance and incorporated lean tools into their evaluation, the audit could have identified opportunities to improve the maintenance of the press and the balance of the production line, while eliminating rejected motors and associated rework. In other words, massive cost savings. If your organization is interested in gaining more than just a certificate from your internal audits, consider adding lean tools to your auditor’s toolbelt.
For more information on Lean, Internal Quality Management Auditing and other training, visit the-center.org or contact The Center at inquiry@the-center.org.
MEET OUR EXPERT
Andy Nichols, Quality Program Manager
Andy has 40 years of expertise in a wide variety of roles and industries, with a focus on quality management systems in manufacturing organizations. In addition to his ISO 9000 Management Systems experience, he has worked extensively with ISO/TS16949, ISO/IEC 17024 and ISO/IEC 17025. His broad practical knowledge of ‘Quality Tools’ includes: SPC, FMEA, Quality Circles, Problem Solving, Internal Auditing and Process Mapping. He also has been an IRCA and RABQSA accredited Lead Auditor.
Since 1991, the Michigan Manufacturing Technology Center has assisted Michigan’s small and medium-sized businesses to successfully compete and grow. Through personalized services designed to meet the needs of clients, we develop more effective business leaders, drive product and process innovation, promote company-wide operational excellence and foster creative strategies for business growth and greater profitability. Find us at www.the-center.org.
Categories: Lean Principles,
Quality Management