9/28/2018
BY: ANDY NICHOLS
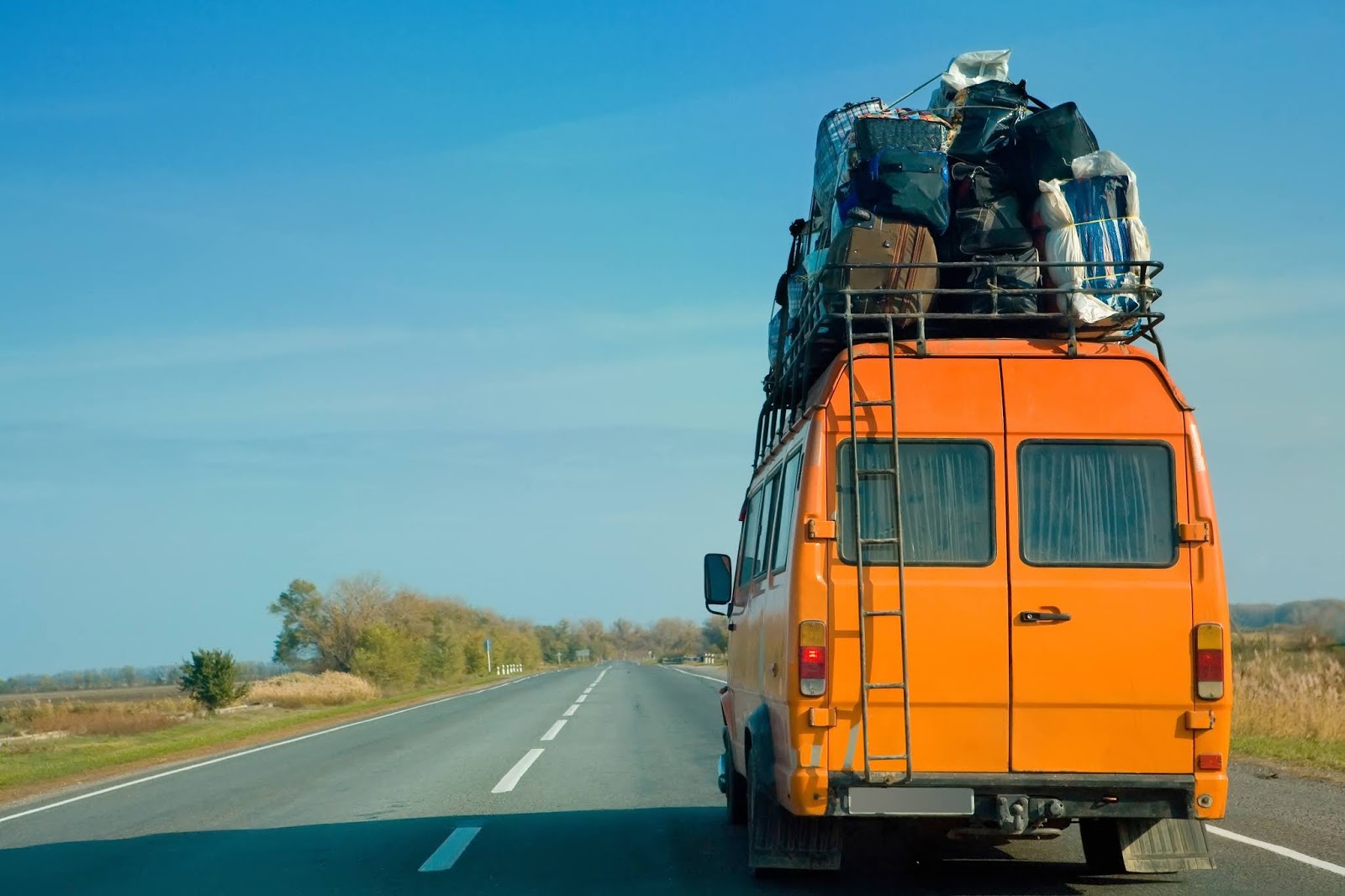
If you are registered to ISO 9001:2015 or one of the quality management requirements built on the international standard, like IATF 16949 or AS9100D, your management must comply with the requirements of the “Management Review” clause 9.3. When complying with this requirement, commonly asked questions include how often and when to do the review. A quick look at the inputs and outputs of the review process doesn’t provide much of a clue to an organization since there is no clearly stated requirement to review those things at any specific time. Fortunately, some guidance can be found in understanding a great American past-time – the road trip!
Frequently the need to comply with this ISO 9001-based requirement is seen only as a way to do what is necessary, without understanding what benefit the activity brings to the organization. In many ways, it’s like the drive to work each day: you have to do it, you don’t have much control over the road conditions or what other drivers do, how long it takes, etc. It’s something you’re forced to endure, and as drivers we often “switch off” or become distracted. We essentially function in “auto pilot,” not investing interest in what we are doing or paying attention to what is happening in front of us. In performing a management review this way, without carefully analyzing the process at each step, your company can miss out on some of the benefits such a review could bring.
This leads us to the question: What is the benefit of an effective review, performed by management, of the Quality Management System?
Answer: To get a balanced view of the “road trip” to ensure all involved are getting the most out of it.
Anyone who has filled a car with people (think Process Owners) and driven any distance will know that although there’s one primary objective - to complete the journey - everyone may have their own specific objectives. These individual objectives may, however, contradict others. For example, the driver has the main objective in mind, but also the objective to obey the posted speed limits. The journey also may call for extra fuel stops because a big vehicle was needed to accommodate everyone. This, in turn, might conflict with others’ objective(s) of meeting their destination in the quickest possible time. Some might have the objective of making the journey as informative as possible, and their sightseeing may conflict with keeping the journey to the shortest time/distance. Of course, a budget has to be established too, which will have to take these competing interests into account.
As with many things in life, compromises must be made in business. Satisfying customers’ needs, complying with regulations, improving efficiency, reducing costs, retaining employees, keeping tabs on key suppliers and so on, all must be balanced in strategic decision making.
If we apply the “Plan, Do, Check, Act” cycle to our road trip, ensuring we plan, understand and accommodate each rider’s requirements for the road trip and set clear objectives and measurables at the outset of the journey, there’s a better chance of meeting all desires of passengers along the way. Waiting until the journey is over to conduct a review of passengers and their objectives might be too late to ensure their needs are met. For example, they all made it to their destination, the driver wasn’t pulled over by the police, riders were comfortable. Some wanted mid-afternoon snacks, but most of the money was spent on lunch and fuel. No money or time was made available for sightseeing.
In the same way, although performing one review of the management system per year may not attract a non-conformity from a Certification Body, in reality it’s not going to be effective from the Process Owners’ points of view. Instead, by performing reviews of the progress being made by each Process Owner at some regularly scheduled event, like refueling or food breaks, adjustments can be made in the moment and everyone has a better chance of meeting their objectives.
If your organization finds it is doing their management reviews just to comply with ISO 9001 requirements, there’s a good chance you have yet to realize the benefits these reviews could bring to your business. Instead of performing annual, rushed reviews simply because “ISO-says-so,” work towards establishing regular reviews to ensure all parties are consistently satisfied and your Quality Management System is running smoothly. With this in place, no one will ever have to ask, “Are we there yet?” again.
For help with understanding how an effective Management Review Process can be established, contact us at inquiry@the-center.org or call 888.414.6682.
MEET OUR EXPERT
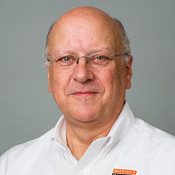
Andy Nichols, Quality Program Manager
Andy has 40 years of expertise in a wide variety of roles and industries, with a focus on quality management systems in manufacturing organizations. In addition to his ISO 9000 Management Systems experience, he has worked extensively with ISO/TS16949, ISO/IEC 17024 and ISO/IEC 17025. His broad practical knowledge of ‘Quality Tools’ includes: SPC, FMEA, Quality Circles, Problem Solving, Internal Auditing and Process Mapping. He also has been an IRCA and RABQSA accredited Lead Auditor.
Since 1991, the Michigan Manufacturing Technology Center has assisted Michigan’s small and medium-sized businesses to successfully compete and grow. Through personalized services designed to meet the needs of clients, we develop more effective business leaders, drive product and process innovation, promote company-wide operational excellence and foster creative strategies for business growth and greater profitability. Find us at www.the-center.org.
Categories: Quality Management