9/20/2013
Have you ever heard of Aesop’s Fables? If you’re unfamiliar, Aesop was a Greek story-teller, credited with sharing a number of short stories containing moral lessons for the listeners. There’s actually a famous fable that applies to manufacturing. It’s called, The Ant and the Grasshopper.
To summarize the fable, there are two animals featured in the plot... and you guessed it…one is an ant, the other, a grasshopper. During summertime, the ant works diligently to prepare for the winter. He spends his time hunting, gathering, storing food, etc.
On the other hand, the grasshopper spends summertime having fun. The grasshopper lounges around, sings and dances with his friends and goes about his days carefree. When winter comes around, the grasshopper is left cold and starving while the ant enjoys his food and shelter.
Moral of the story: plan ahead.
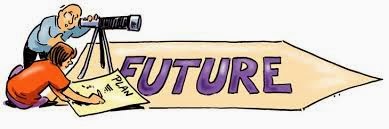
Like any good boy scout, being prepared gives you the ability to respond well in any given circumstance. In business, there are events that are out of control. Disasters or crises unexpectedly occur and negatively impact our business. While a loss of revenue or damage of some sort may be inevitable, we can minimize the impact if we plan ahead. This is why business continuity planning is so important.
Business continuity planning outlines the actions a manufacturer takes when operations are threatened by crises. The plan gives your team an organized path on how to move forward both internally and externally.
Look, we like to be optimistic and celebrate the successes of manufacturers. However, we also need to prepare for the worst. Think about the following scenarios:
- How would you communicate with your clients if a natural disaster knocked your electricity out for a week? Who’s responsible for contacting clients? For contacting employees? What about vendors? Deliveries?
- Do you have a statement prepared for the public in the case of a product recall?
- Do you have internal standard operations in place to manage a recall of equipment or parts?
- Do you have alternatives in place in the event of a supplier disruption?
- What is the “chain of command” if there was a disaster preventing your team from coming into work?
- Does everyone on the team know their responsibilities in the case of a crisis? When did you last update the plan? Practice it? Do key team members still work here?
There are many benefits to planning ahead. Foremost, it helps keep your team safe. When everyone is organized and on the same page, it limits panic and hysteria. This is of the utmost importance. Internally, giving team members their specific role, and then implementing the plan with annual drills, brings confidence in a crisis that also enables them to feel like they are a part of the solution, building teamwork and morale.
You may have to “eat some costs” during a disaster, but effective business continuity planning and implementation also helps you avoid or minimize a major loss in revenue. Wasted time and resources attempting to recover in hysterics = a waste of money.
How you handle unfortunate circumstances also influences how the public and your customers perceive your organization. To this day, colleges and universities still use the Tylenol disaster in the 1980’s as a case study for effective crisis planning. In the 1980’s, someone had poisoned Tylenol pill tablets resulting in customer deaths. This was a horrible tragedy and something out of their control. However, Johnson & Johnson had such an effective plan in place that they were able to rapidly recall their products and introduce new safety features immediately into the market. The company quickly regained the public’s trust and their safety features are used as the standard today.
Don’t be the grasshopper of manufacturing. Business continuity is important and shouldn’t be overlooked. If you would like assistance, please contact us at inquiry@mmtc.org.
Since 1991, MMTC has assisted Michigan’s small and medium-sized businesses compete and grow. Through personalized services fitted to meet the needs of clients, we develop more effective business leaders, drive product and process innovation, promote company-wide operational excellence and foster creative strategies for business growth and greater profitability. Find us at www.mmtc.org. (Image Source)
Categories: Continuous Improvement