11/4/2022
BY: ANDY NICHOLS
Since its first publication in 1987, the International Standard for Quality Management Systems known as “ISO 9000” has been plagued by many myths. As with all mythology, there are narratives and beliefs which have become almost foundational to the implementation of the ISO 9001 requirements. Like classical myths, those associated with ISO 9001 frequently become rituals which are implemented in the organization’s Quality Management System and become sacrosanct.
During the past 35 years, the ISO 9001 requirements have been revised a few times and with each edition new myths have been created. In particular, the revision published in 2015 caused a great commotion regarding the inclusion of the word “risk” and the complete removal of references to any specific types of documentation. These myths which have been created and promulgated are due, in no small part, to the widespread adoption of the international standard around the world and the requirement to be certified in ISO 9001 as a prerequisite to doing business. This second reason led to the most widely known myth, that doing ISO means, “Say What You Do and Do What You Say.”
It is thought that this snappy aphorism came from DuPont de Nemours Corporation since they were one of the first U.S.-based corporations to become ISO 9001 certified. The origins of this myth come from the popularly held understanding that ISO 9001 required a documented procedure for each requirement (it didn’t) and that the certification auditors would be looking for those procedures to describe what was being done to create products, etc. This single myth was, alone, responsible for causing the over-documentation of an organization’s Quality Management System (QMS), which was justified by the trope, “We can still operate if no one turns up for work tomorrow.”
In addition to over-documenting its QMS, it became clear that organizations that achieved ISO 9001 certification didn’t necessarily improve their quality performance. In a famous product quality lawsuit between a car maker and a tire supplier, a top newspaper published the myth that ISO certification would “Allow Concrete Life Preservers to be Made.” This, of course, was superficial in the extreme.
Many myths stem from what organizations experience when undergoing an ISO certification audit. Commonly held myths include:
-
Annual calibration of all measuring equipment
-
Calibration stickers on equipment
-
Approval signatures on documents
-
Management review meetings performed at least annually
-
All ISO requirements internally audited in a year
-
Internal auditors who are “independent” of the function they audit
-
Documents bearing their status as “controlled/uncontrolled”
-
Non-conforming product should be locked up to prevent use
It should come as no surprise when reading through the ISO standard’s requirements, (it’s only 37 pages cover to cover, and the requirements are described in 20 of them) none of these things are mentioned. ISO 9001 simply states what is required to be present in an organization’s Quality Management System, not HOW to implement those requirements, and it’s usually in the implementation of the QMS these myths cause most havoc.
If your organization is implementing an ISO 9001-based Quality Management System (including AS9100D and IATF 16949) and you’d like to know how to avoid such myths, The Center’s experts are here to help.
Register for an upcoming Quality course and
contact us to get started on implementation.
MEET OUR EXPERT: Andy Nichols, Program Manager
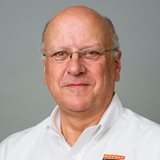
To The Center’s clients, Andy Nichols, CQP MCQI, brings 40 years of expertise in a wide variety of roles and industries, with a particular focus on quality management systems in manufacturing organizations. Prior to joining the Michigan Manufacturing Technology Center, he was the East Coast Regional Sales Manager for NQA, a “Top 5” Global Certification Body, responsible for significant sales growth in a highly competitive marketplace. He has authored two books, “Exploding the Myths Surrounding ISO 9000 – A Practical Implementation Guide” (published by ITG in April 2013) and “A Guide to Effective Internal Management Systems Audits" (published May 2014).
Since 1991, the Michigan Manufacturing Technology Center has assisted Michigan’s small and medium-sized businesses to successfully compete and grow. Through personalized services designed to meet the needs of clients, we develop more effective business leaders, drive product and process innovation, promote company-wide operational excellence and foster creative strategies for business growth and greater profitability. Find us at www.the-center.org.
Categories: Quality Management