11/2/2018
BY: ANDY NICHOLS
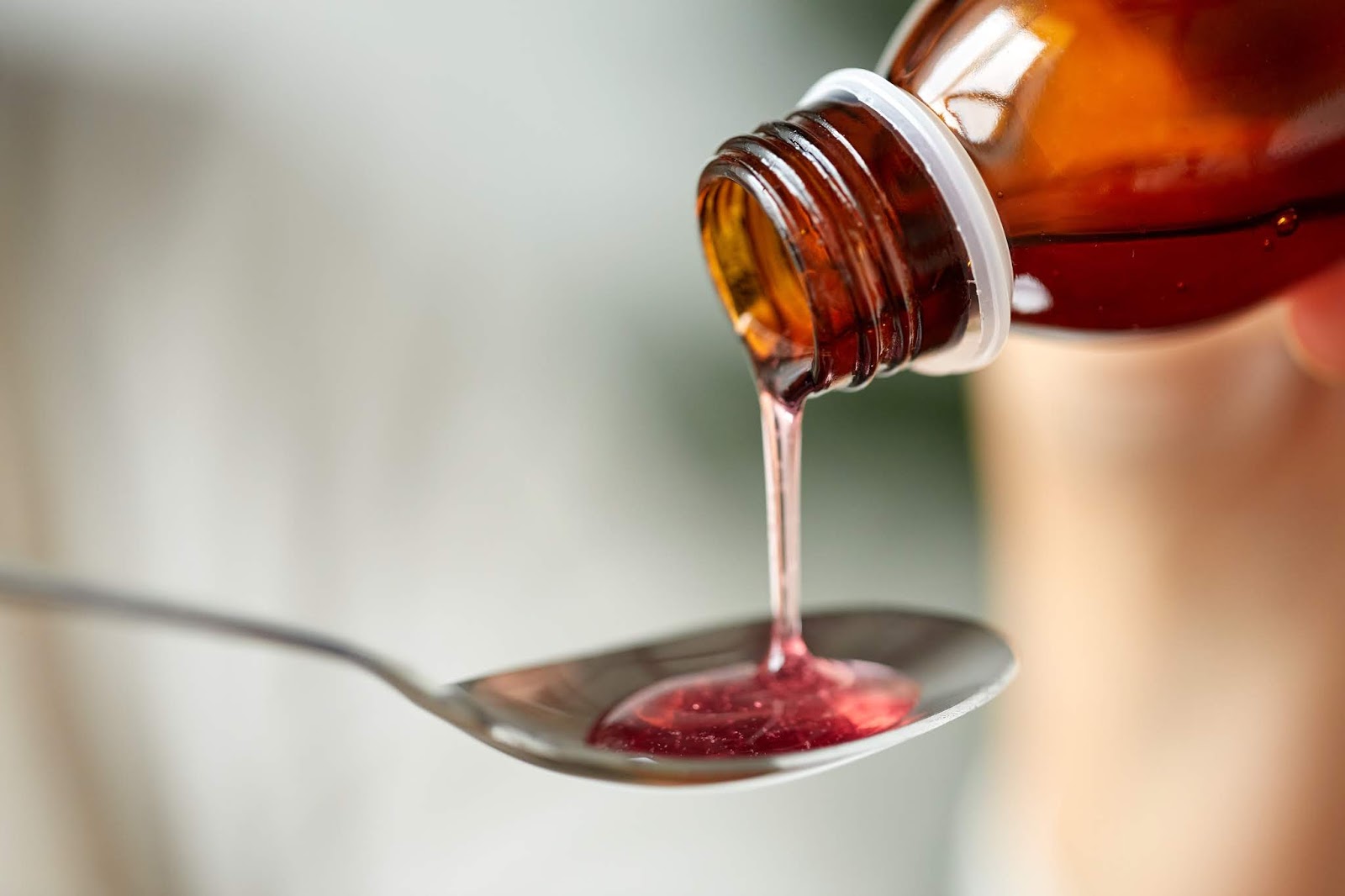
The medical device industry is ill! According to the FDA’s medical device recall data, this year alone there have been 22 recalls, tarnishing thousands of medical products. Research also has shown that most of these recalls came from manufacturing-related defects, making this a critical issue for medical device manufacturers to tackle. Recalls like these are costing the industry between $1.3 and $5 billion each year and cause patients much frustration, time and pain. These defects are not like normal manufacturing defects as any mistake in production could lead to serious, and even life-threatening, issues for patients. Imagine having to replace a defective knee joint two or even three times!
Clearly, something must be done to improve the industry’s performance. A solution is now available through a recently launched accreditation program called MedAccred. Similar to traditional Quality Management Systems audits but much more focused in scope, MedAccred aims to eliminate defects at the source by improving manufacturing processes to ensure patient safety. A MedAccred “Critical Process Assessment” involves a deep dive on processes where normal, non-destructive inspection and testing cannot be used to determine quality. Currently, MedAccred offers accreditation programs for the following critical processes:
- Cable & Wire Harness
- Heat Treating
- Plastics Extrusion
- Plastics Injection Molding
- Printed Circuit Board Assembly
- Sterilization
- Welding
- Printed Boards
Creating the Cure
Organized by the Performance Review Institute (PRI), MedAccred closely mirrors the well-established NADCAP program used in the aerospace and defense manufacturing sector. Each program takes an in-depth look at processes to ultimately identify and eliminate sources of error in production. Evidence of the effectiveness of this method has already been seen in companies that achieved NADCAP accreditation. For example, in 2010 the DuPuy Synthes division of Johnson & Johnson observed a more consistent and higher quality result of heat treatment services from a supplier that held NADCAP accreditation. At about the same time, the FDA took an increased interest in the performance of medical device manufacturing quality and identified MedAccred as the ideal program approach to support.
Since then, Stryker, Medtronic, Boston Scientific, Baxter and Philips Healthcare have joined Johnson & Johnson in flowing down the MedAccred requirements as part of their procurement criteria when awarding new/repeat business, making MedAccred accreditation essential for both minimizing defects and maintaining a competitive edge.
As the NADCAP experience has proven valuable, it is expected that the MedAccred program will make a substantial in-road to improving medical device quality. After all, we rarely hear of an aircraft falling from the sky, and modern jet engines are now so reliable that it is common for intercontinental aircraft to have only two engines, rather than the norm of four. With the importance of medical device quality reaching critical heights, manufacturers now can strive to achieve this same level of dependability and safety in products through MedAccred accreditation.
A Spoonful of Sugar
Unlike an ISO-type Management Systems audit, the MedAccred assessment is carried out using a highly detailed checklist and is performed by a Subject Matter Expert, fully familiar with the target process. Following a two-step procedure, the assessor first takes a look at the process documentation (organizations must be ISO 9001/ISO 13485 Certified as a prerequisite) then observes the actual practices on the manufacturing shop floor. During this observation, a number of employees are interviewed to gain a perspective on their knowledge of the process, its controls and likely defects. In addition, the controls on products supplied to the organizations, such as raw materials and components, are closely reviewed. The results of the assessment are then reported to a PRI technical committee for review/action.
Schedule Your Physical
Once an organization decides to pursue MedAccred accreditation, some preparation will be necessary. A Gap Assessment and Plan of Action is a good place to begin, and The Center can assist with this step. Our PRI-trained and MEP Certified SMEs are available to walk an organization through the complexities of the assessment checklist and help identify any areas that require work, advise as needed on closure of the gaps and perform the required internal assessment before the PRI assessor arrives.
With patient safety and future contracts at risk, the time is now to gain accreditation. For further details on how The Center’s SMEs can assist with preparing for MedAccred accreditation, visit the-center.org or call 888.414.6682.
MEET OUR EXPERT
Andy Nichols, Quality Program Manager
Andy has 40 years of expertise in a wide variety of roles and industries, with a focus on quality management systems in manufacturing organizations. In addition to his ISO 9000 Management Systems experience, he has worked extensively with ISO/TS16949, ISO/IEC 17024 and ISO/IEC 17025. His broad practical knowledge of ‘Quality Tools’ includes: SPC, FMEA, Quality Circles, Problem Solving, Internal Auditing and Process Mapping. He also has been an IRCA and RABQSA accredited Lead Auditor.
Since 1991, the Michigan Manufacturing Technology Center has assisted Michigan’s small and medium-sized businesses to successfully compete and grow. Through personalized services designed to meet the needs of clients, we develop more effective business leaders, drive product and process innovation, promote company-wide operational excellence and foster creative strategies for business growth and greater profitability. Find us at www.the-center.org.
Categories: Medical Devices,
Quality Management