11/3/2017
BY: ANDY NICHOLS
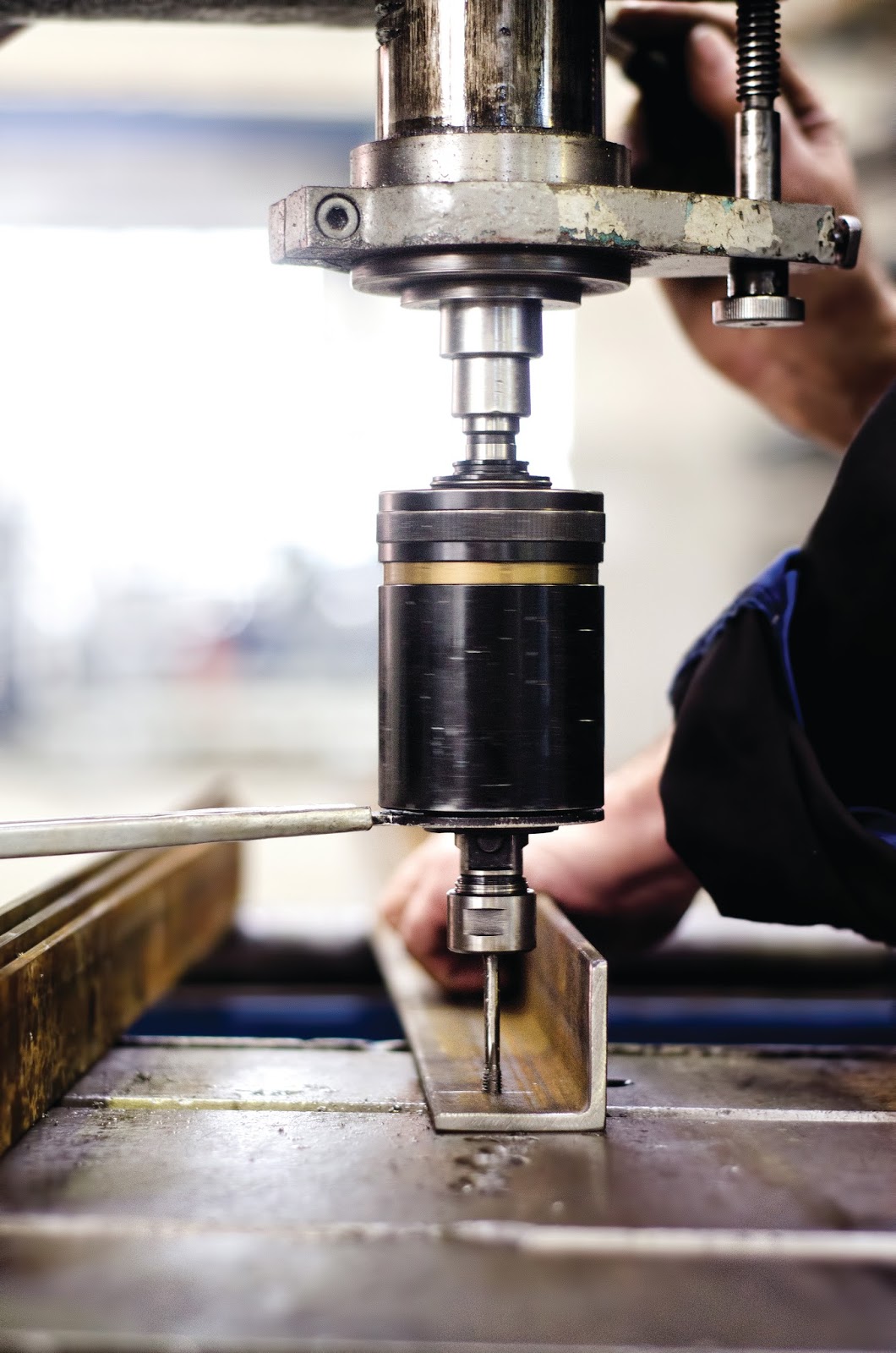
One of the first things that comes to mind when describing Quality Management Systems and “ISO 9000” is documentation, which often includes a Quality Manual. The background to Quality Management Systems started with big procurement organizations such as government agencies and Fortune 500 companies making Quality Systems a contractual requirement. Frequently, these requirements included the need for a document, often referred to as a “Quality Manual,” a “Quality Plan” or similar. These were used by a supplier to describe the approach prescribed to fulfill the contract requirements and assure the quality of the deliverables.
Today, a hallmark of ISO 9001 Quality Management Systems documentation is a Quality Manual, and documents of this type have been a requirement of the International Standard since 1987. Manuals produced by many organizations emulate the format and content of the ISO 9001:2008 clauses (4 through 8) to the extent that the words “The organization shall” have simply been replaced by the name of the company! This often leads to documents that run onto 25 or more pages, written in cryptic terminology which has little relevance to the business of the organization. The result? People rarely read the document, and it’s often only rubber stamped by auditors before gathering dust on an office shelf somewhere…
Amazingly, the 2015 edition of ISO 9001 dropped the requirement for a quality manual along with any type of traditional quality documentation. This included procedures, work instructions, etc., leaving it up to the organization itself to determine what it needs based on understanding customers, regulatory expectations, and its own requirements for documenting.
Based on their experience with Quality Manuals, it might be tempting to an organization to discard theirs as, after all, it only sees the light of day when the Registrar auditor is on site – and no-one else reads it.
But wait! Before that proverbial baby is discarded with the bath water, why is it that no-one reads the Quality Manual? Maybe it’s because it’s not helpful, uses arcane language, and is formatted on an ISO document which no one has reason to read!
There’s a better model on which we can base our Quality Manual which might bring some help to users: The “Quick-Start Guide” you get with some items of household electrical equipment, for example, is a clue. These guides cover the basics of what the new user needs to know in order to get “up and running.” For more detailed descriptions, including navigating the complete set of functions, features, and fault finding, reference can be made to the more comprehensive manual which is also included.
Will your upgrade to the 2015 ISO 9001 requirements be heralded by a new, useful Quality Manual “Quick Guide to the Quality System”? You decide. If you’d like to learn more about the format and content of such a document, contact our Quality Team at
ISO@the-center.org.
MEET OUR EXPERT
Andy Nichols, Quality Program Manager
Andy has 40 years of expertise in a wide variety of roles and industries, with a focus on quality management systems in manufacturing organizations. In addition to his ISO 9000 Management Systems experience, he has worked extensively with ISO/TS16949, ISO/IEC 17024 and ISO/IEC 17025. His broad practical knowledge of ‘Quality Tools’ includes: SPC, FMEA, Quality Circles, Problem Solving, Internal Auditing and Process Mapping. He has also been an IRCA and RABQSA accredited Lead Auditor. To read Andy's full bio, visit click here.
Since 1991, the Michigan Manufacturing Technology Center has assisted Michigan’s small and medium-sized businesses to successfully compete and grow. Through personalized services designed to meet the needs of clients, we develop more effective business leaders, drive product and process innovation, promote company-wide operational excellence and foster creative strategies for business growth and greater profitability. Find us at www.the-center.org.
Categories: Quality Management