5/4/2018
BY: CHUCK WERNER
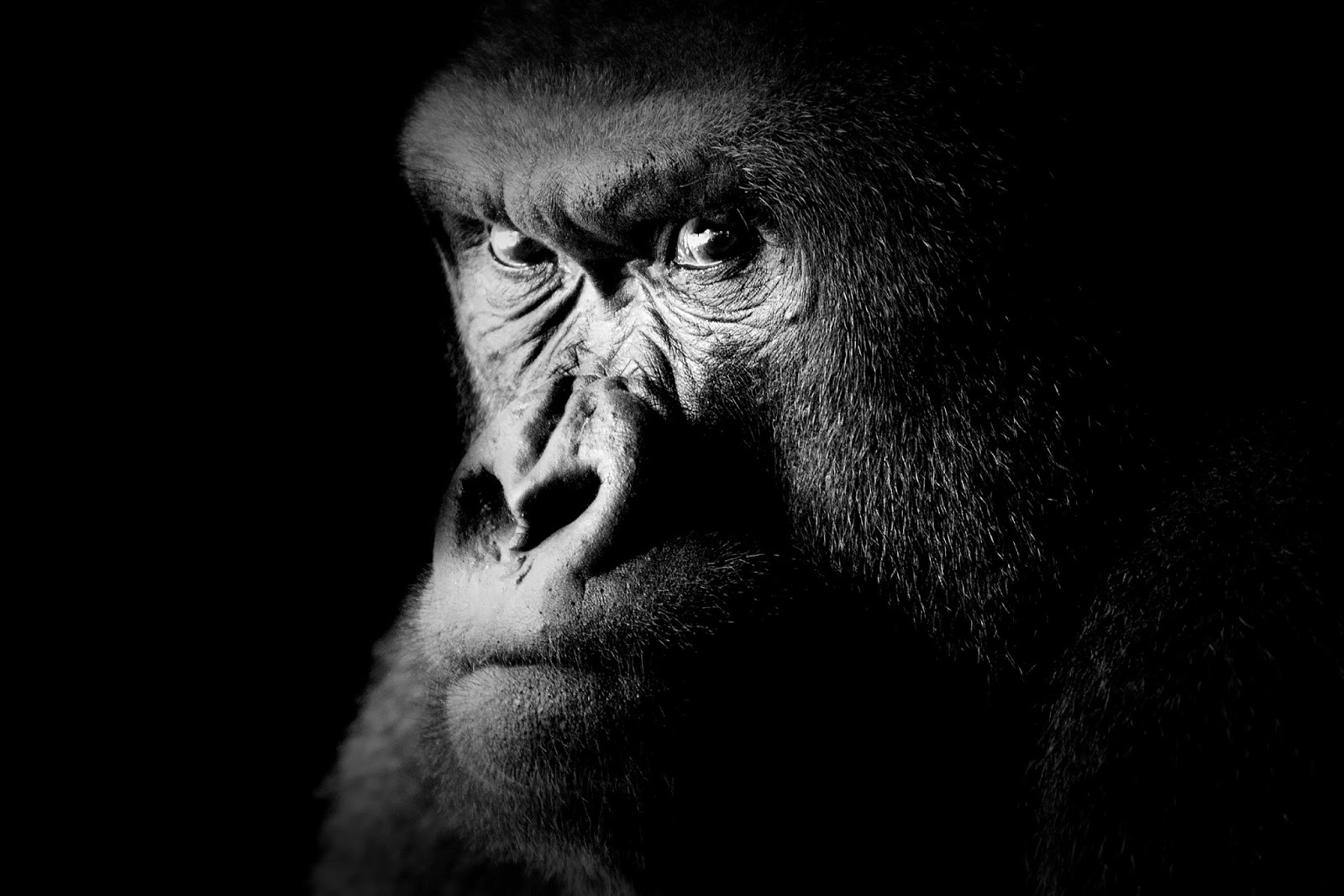
Discussions of the Industry 4.0 technologies among small to medium enterprises usually take one of two paths. The first is a politely positive path where everyone ignores the impact these advancements will have on the human workforce. This is what is known as ignoring the “elephant in the room,” where there is an obvious problem at hand, but no one wants to address it.
The other is usually approached more fearfully, as if we were crawling into a cage with a seething Silverback. Down this path, we are often keenly aware of the presence of this “800-pound gorilla,” but we feel utterly powerless to do anything about it. As we see it, the robots are waiting to take everyone’s jobs and we the “people” will be completely displaced.
In each of these approaches, nobody wins. Refusing to talk about something never results in a resolution, while ignoring it out of fear poorly serves both the business and the people who are part of it.
The truth is, there are some jobs where machines cannot compete with a human, and it will be a long while before they can. Frankly, there are some jobs where the cost to automate does not provide a sufficient return on investment to make it worthwhile. Also, robots cannot match the dexterity of a human. Operations that require fine manipulation and sensitivity are still beyond the ability of any automaton. Additionally, many jobs require critical thinking, judgement and the ability to react to unusual outcomes. It is true that analytics have come a long way, but most examples of “artificial intelligence” are still just programmed responses defined by expected inputs. Humans are much better at handling the unforeseen and possess a greater ability to adapt and overcome. Lastly, most people are still vastly superior at interacting with their fellow humans. When was the last time you enjoyed hearing “Press 1 for…”?
On the other hand, there are jobs where automation makes sense. Tasks involving simple repetitive movements, harsh environments, heavy lifting and poor ergonomic positions are prime candidates for the application of robotics. These are often positions where companies have difficulty hiring or in which they see high turnover. These jobs lack the ability to challenge and stimulate the human mind. Other times the low rate of pay offered to perform such simple tasks makes them unappealing. In regions where competition for dependable employees is high, these jobs are not seen as promising enough to entice potential employees to relocate. Lastly, many millennials are simply not keen on the idea of factory work.
Automation-friendly jobs also include those primarily composed of non-value-added activities. Transporting or moving an object from point to point – or a “lift and tote” job – is one example. Another is sending someone out to collect information or “go and see.” The use of technology and analytics not only provides real-time data, but also presents the information in a usable format to decision-makers without long hours of entry and analysis. Freeing employees from performing these wasteful tasks allows them to spend their time on more value-added functions. It also enables them to perform a function at which the human mind excels: identifying and implementing improvements to a product, process or service.
Some jobs will continue to be performed by humans as much as they always have. Or, they will still be performed by people, but with assistive technology to allow for greater effectiveness and efficiency. And, as time goes on, and technology continues to improve, and the cost to implement it continues to decrease, some jobs will be given over to automation. Ignoring this fact will only put your company at a disadvantage.
There are several things that any business should be doing to prepare for success in these ever-changing times:
The management team should take an honest look at what isn’t – but should be – happening around the workplace. It isn’t unusual for activities like equipment upkeep, training, auditing, quality checks and other important tasks to be postponed or even ignored in the face of task saturation or trying to ensure on-time delivery. Additionally, most people find themselves so busy working in the process that they are never able to identify time to work on it. Technology provides the opportunity to eliminate these non-value-added and time-consuming tasks. This time can then be invested in enabling team members to focus on the upkeep, control and improvement of product or process.
Within the company, the leadership team will want to invest in improving the skillsets of their team members. In some instances, the implementation of technology will create the need for new positions to install, operate and maintain it. Support and mentoring will also need to be provided for the workforce to be able to capably adopt and utilize these technologies. More importantly, the goal is to elevate the work force from mere process operators to creative process improvers. This may require additional training and skills that may not have been provided to front-line positions within the organization. Skills like root cause analysis, lean tools, and process improvement will be needed in the advanced manufacturing environment.
On a larger scale, businesses will need to partner with local educational entities to promote interest and training on STEM (Science, Technology, Engineering, Math) skills for our future workforce. The mismatch in demand versus supply of these abilities is already creating many employment gaps. Studies show that there will be roughly one million programming jobs unfilled by the year 2020. The construction industry anticipates around the same number of positions available in that same timeframe. And the benefit isn’t just in those industries or simply with jobs involving STEM skills. Studies also estimate that for every STEM-related job created, 4.3 jobs in local goods and services industries are generated.
If businesses choose to ignore their elephants or gorillas (or lions or tigers or bears – oh my), one thing is certain: others will collect on the opportunities these new technologies provide and become dominant in their fields. But if you engage now and employ those assistive technologies that make good business sense for you, your company will not only achieve success for the business but provide greater job satisfaction for the teams. You also will help pave the way for the workforce of the future.
To learn more about how Industry 4.0 technologies can work with your company rather than against it, come to The Center's free Industry 4.0 EXPLORE event on May 10 from 8:30am to 10:30am.
MEET OUR EXPERT
Chuck Werner, Lean Program Manager
Chuck has been a Lean Program Manager at The Center since 2016. His areas of expertise are in Lean, Six Sigma and Quality. Chuck has devoted many years to practicing Six Sigma methods, ultimately earning a Six Sigma Master Black Belt in 2011. He is passionate about helping small and medium-sized manufacturers become more prosperous using a variety of tools and methods gathered from over 27 years of experience. Additionally, Chuck is a certified ISO/QS9000 Lead Assessor, Training Within Industry (TWI) Master Trainer and is certified in OSHA Compliance and Accident Reduction.
Since 1991, the Michigan Manufacturing Technology Center has assisted Michigan’s small and medium-sized businesses to successfully compete and grow. Through personalized services designed to meet the needs of clients, we develop more effective business leaders, drive product and process innovation, promote company-wide operational excellence and foster creative strategies for business growth and greater profitability. Find us at www.the-center.org.
Categories: Advanced Manufacturing,
Industry 4.0,
Smart Manufacturing,
Workforce