5/6/2016
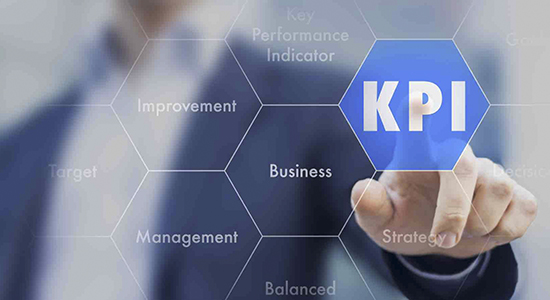
Key Performance Indicators (KPIs) are essential tools used in manufacturing management. These metrics can be used to measure the overall success of an organization or manage daily functions. Measurements help determine if operations are effective or if changes need to be made in order to avoid future inefficiencies and problems.
Which KPIs will help better manage business operations and become more efficient? Well, every aspect of the manufacturing process can be measured! It is important to quantify meaningful indicators that help the organization achieve its goals. Information is only valuable if it is used correctly to improve operations.
Examples of KPIs in Manufacturing
Hundreds of data sources are usually available, but too much information gets overwhelming. Below are some examples of the most commonly used KPIs in manufacturing.
- Count – The amount of product produced.
- Reject ratio – The ratio of unacceptable units resulting in scrap.
- Rate – How fast or slow machines produce goods.
- Target – Goals for rate and quality.
- Takt time – The length of time to complete a task (the average time between the start of production of one unit and the start of production of the next unit).
- Overall Equipment Efficiency – Measures resource utilization.
- Downtime – Any time the machines are not running.
KPIs measure efficiency, effectiveness and capability. All of these measures are quantifiable and meaningful. Ideally, they should help drive the decision-making process leading to continuous process improvement. Lagging indicators are typically “output” oriented, easy to measure but hard to improve or influence. Leading indicators are input oriented, hard to measure and easy to influence.
Getting Started
- Use operational goals to strategically decide what indicators to monitor. Many companies attempt to monitor too many indicators and begin to suffer from “paralysis by analysis”.
- Decide who will be using this information and what level of detail each user will have access to. Not all users require the same level of detail. Some may only need a high level overview while others need advanced analytical functionality.
- Information is only valuable if it is used, and it must be presented in a way that is easily understandable to the user. Dashboards are popular presentation methods.
- Following a “Plan-Do-Study-Act” format, make use of this new information. This process should be consistently and appropriately used in decision-making.
In order to successfully use KPIs, all metrics must be shared with employees since they must know how they are being measured. Management needs to know how each area is performing, but complete awareness and effectiveness only occurs if the metrics are shared at the front line. Otherwise, management has an impressive array of numbers and a great deal of knowledge but no real change in operations. Measuring for the sake of measuring is wasteful if it does not provide value. Do not get carried away by the numbers!
KPIs and Continuous Improvement
KPIs are a great guide when attempting to transform a business, especially during Lean and continuous improvement initiatives. They provide the baseline for any subsequent improvement and measure business process improvement.
MMTC can assist your company in deciding which KPIs to study to meet organizational goals. For more information about our Lean Business Solutions, contact the Michigan Manufacturing Technology Center at 888-414-6882 or click here.
Since 1991, MMTC has assisted Michigan’s small and medium-sized businesses successfully compete and grow. Through personalized services fitted to meet the needs of clients, we develop more effective business leaders, drive product and process innovation, promote company-wide operational excellence and foster creative strategies for business growth and greater profitability. Find us at www.mmtc.org.
Categories: Continuous Improvement