3/1/2019
BY: ANDY NICHOLS
Most of us are familiar with the famous Pyramids of Giza
in Egypt. Built 4,500 years ago, more than 118 of these structures have withstood the test of time and stand as a testament to the amazing engineering and construction skills of the day.
Now, fast forward to 1987. ISO 9001 was released with the visual metaphor of a pyramid often being used to represent the documentation requirements of the standard for Quality Management Systems (QMS). Despite not being a model directly described in the ISO standard or any related guidance, like ISO 9004, some quality teams preferred to envision the hierarchy of documents mentioned in ISO 9001 as a pyramid, much like the one below.
This pyramid metaphor did, indeed, come from a suggestion that there are “layers” of documentation required in a QMS. Early versions of ISO 9001 specified a procedure as a requirement for nearly every “clause,” with no reference to documentation. Clause 4.9 went on to define the requirements for control of an organization’s production processes as the option of “...documented work instructions, where the absence of such would adversely affect quality.”
This is the only clause that mentions the option of documenting work instructions. No additional documentation was mandated for the procedures for “Contract Review,” “Purchasing,” “Corrective Actions,” etc. This oversight, likely exacerbated by the mantra, “Say what you do, do what you say,” resulted in people creating more documentation than was required, either by the standard or by the organization.
As with the Pyramids of Giza, the visual metaphor seemed set to withstand the changes through which ISO 9001 has undergone (in 1994, 2000 and 2008). Not so!
In 2015, ISO 9001 went through a seismic event which should have toppled the documentation pyramid. After 30 years of use, there is no prescriptive requirement for:
- A Quality Manual
- Documented Procedures
- Work Instructions
With ISO 9001:2015, it is now left up to the organization to determine which documents it believes it needs (considering factors such as “interested parties,” “organizational knowledge,” etc.). This significant change to the foundation of the QMS was partly inspired by feedback from small organizations who felt they did not need to rely heavily on writing down their processes to function effectively.
Unlike the Pyramids of Giza, which see thousands of visitors a year, an organization usually doesn’t entertain the same interest in its QMS documentation. Although no one expects employees to eagerly line up to read the quality manual or put the Corrective Action procedure on their “must-read" list, the simple fact is that a significant majority of Quality Management documents go unused.
There are many valid reasons for this, including:
- Quality Manuals are written to rephrase the ISO 9001 requirements
- Procedures don’t describe processes
- Work instructions are written without involvement from the people doing the work
The latest revision of ISO 9001 gives all organizations an opportunity to revisit the purpose of their Quality Management documentation in achieving their goals and strategic objectives. After all, we equip our people with tools and machines to make their work more effective and efficient – shouldn't we do the same with their documentation?
Let’s not bury our people in documentation pyramids like the ancient Egyptians did to their pharaohs!
MEET OUR EXPERT
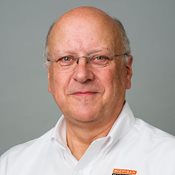
Andy Nichols, Quality Program Manager
Andy has 40 years of expertise in a wide variety of roles and industries, with a focus on quality management systems in manufacturing organizations. In addition to his ISO 9000 Management Systems experience, he has worked extensively with ISO/TS16949, ISO/IEC 17024 and ISO/IEC 17025. His broad practical knowledge of ‘Quality Tools’ includes: SPC, FMEA, Quality Circles, Problem Solving, Internal Auditing and Process Mapping. He also has been an IRCA and RABQSA accredited Lead Auditor.
Since 1991, the Michigan Manufacturing Technology Center has assisted Michigan’s small and medium-sized businesses to successfully compete and grow. Through personalized services designed to meet the needs of clients, we develop more effective business leaders, drive product and process innovation, promote company-wide operational excellence and foster creative strategies for business growth and greater profitability. Find us at www.the-center.org.
Categories: Quality Management