6/16/2023
BY: BOB JENKINS
To strengthen designs and decrease failures, IATF 19649:2016 requires design engineers to be competent in Design for Manufacture (DFM) and Design for Assembly (DFA). This standard has greatly improved manufacturing with an increase in mistake-proofing features. Consistent third-party audits of the standard’s section 8.3 and questions about a designer’s background in DFM and DFA have continued to improve the process.
Rather than worrying about the number of errors, designers can concentrate on efficient manufacturing. When it’s not possible to build an error, you won’t get as many. More thought going into possible errors in manufacturing could make DFMEA (Design Failure Modes and Effects Analysis) more effective. In the past, the only design FMEA thought was, “What will fail given the materials I’m using and the method of assembly?” It was a, “What will happen to the customer?” position. There isn’t anything wrong with that, but the other customer is important, too.
WORKING TOWARDS ZERO DEFECTS
So, we’ve reached the level of zero defects that was thought to be unobtainable when W. Edwards Deming first came to Ford Motor Company after his work in Japan. When Don Peterson invited him to help Ford improve, the industry was measuring warranty in R/1000. When measuring shifted to PPM (parts per million defective), which decreased allowable failures by 1,000 times, no one believed it could be done. A few years ago, GM started using PPB (parts per billion), which tells everyone, “We don’t want to see any defects.” The zero defects concept is real.
At first, zero defects were thought to be a myth. The Toronto Sun Times even published an article about zero defects and how impossible it would be to achieve. They told a story of IBM sourcing an order for 10,000 circuit boards to Japan. The article used the common (at the time) method of quoting MIL Spec 105D. This standard provided rates of failure within lots that would be considered acceptable. It went on to say, “It is considered acceptable to have three defective boards in the 10,000-lot batch.”
When the completed order arrived at IBM, they opened the box of 10,000 circuit boards and found a note. It read, “We Japanese have a hard time understanding North American business practice, but the three defective boards are included and wrapped separately. Hope this pleases.”
EXPANDING WITH GD&T
From that experience, we see that accomplishing zero defects is a mindset. But I don’t want to sidetrack the true point of this short blog. The intent here is to expand DFM. Certainly, it’s best to include elements that avoid creating a bad part, but what also needs to be included are elements that give manufacturing the opportunity for variability when it can be afforded. To fully incorporate that as a design option, all designers need to understand geometric dimensioning and tolerancing (GD&T).
GD&T, in its most obvious form, has a square specification for a round hole. If that doesn’t seem obvious to you, a GD&T basics class is in order. The language of GD&T allows designers to “say what they mean” on their drawings in a manner consistent across the industry. The uniformity in drawing specifications and regulations reduces guesswork, controversy and assumptions that may be made in the manufacturing process - leading to zero defects.
However, to sustain strength, GD&T would need to be included specifically in the next iteration of the IATF 16949 standard alongside the DFM and DFA requirement for competence for design engineers. If design engineers learn how much they can help manufacturing and how much better the produced product can be, I’m certain they would all want to migrate to GD&T.
GD&T AT THE CENTER
At the Michigan Manufacturing Technology Center, our experienced trainers focus on the most important information to offer you the highest quality
GD&T services possible! Our course materials were developed by Alex Krulikowski, a recognized expert in the field of Geometric Dimensioning and Tolerancing and are taught by our experienced instructors.
Contact us today to see how The Center can help your team learn GD&T.
MEET OUR EXPERT: Bob Jenkins, Quality Program Manager
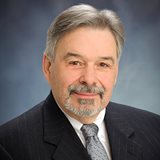
Bob Jenkins is a Quality Program Manager at The Center. In his role, he manages and delivers training and implementation assistance to organizations in the field of quality improvements. As an Exemplar Global Certified Auditor, Bob assists clients with Quality Management System implementations such as ISO 9001:2015 and IATF 16949. He provides internal auditor training and consulting services for various groups, including production, production management and corporate management, in disciplines involving the automotive core tools of quality systems consisting of FMEA, PPAP, APQP, SPC, MSA, and Root Cause Analysis/Problem Solving.
Since 1991, the Michigan Manufacturing Technology Center has assisted Michigan’s small and medium-sized businesses to successfully compete and grow. Through personalized services designed to meet the needs of clients, we develop more effective business leaders, drive product and process innovation, promote company-wide operational excellence and foster creative strategies for business growth and greater profitability. Find us at www.the-center.org.
Categories: Continuous Improvement,
GD&T,
Manufacturing,
Quality Management