6/2/2023
BY: ANDY NICHOLS
Third-party certification of organizations was initiated a few years after ISO 9001 was first published in 1987. In those early days, ISO 9001, 9002 and 9003 were intended to be used to help ensure the quality of products being purchased. Note that ISO 9003 was discontinued.
Instead of a supplier being obligated to implement a Quality Management System (QMS) meeting all ISO 9001 or 9002 clauses, the customer contract might emphasize key requirements contributing most to product quality. If the accurate measurement was critical to meeting part specifications, a system of gauge calibration would be written into the agreement. For example, welder certifications could be required for certain metal-fabricated products. These aspects would become part of a “quality plan,” using the ISO standard as a foundation.
In the UK, many supplier organizations found themselves being audited by multiple government procurement agencies. It was determined that a system of independent audits could be used to control costs and disruptions using ISO 9001 as audit criteria to reduce the burden on taxpayers. Certification bodies, as they were known, sprung from the roots of organizations already familiar with product certification. Many of these organizations had industry-wide recognition - Lloyds Register of Shipping (LR), British Standards Institution (BSI) and British Approvals Service for Cables (BASEC) - and were experienced in performing audits of documented systems. The American Bureau of Shipping and Underwriters Laboratories were early US-based certification bodies also known as “registrars.”
Today, research shows that a major IAF accreditation body, American National Accreditation Body, accredits 75 conformity assessment bodies for ISO 9001. That’s an overwhelming choice and care should be taken to ensure a good “fit” for your organization. Here are some considerations to help select the right conformity assessment body (CAB) for your company:
-
Which CAB certifies your customers?
-
Which CAB specializes in your industry type?
-
Which CAB has a good track record and reputation?
-
Which CAB takes time to ensure their auditors are competent?
Since many CABs utilize contractors to perform certification audits, the location of the HQ plays little/no role in things such as reducing travel costs. Auditor availability is mostly dependent on things like schedule, industry knowledge and the auditor’s interest in the assignment.
To learn more about what’s involved in your organization becoming ISO 9001 certified, stay tuned! Future articles will cover managing the relationship with your conformity assessment body.
ISO CERTIFICATION AT THE CENTER
There are two primary benefits associated with being ISO certified: a competitive advantage and the discipline necessary for future growth. Many companies expect their suppliers to have some form of ISO certification. Without this certification, suppliers are unlikely to even be considered. To help companies be successful, The Center’s experts assist manufacturers in integrating their QMS/EMS objectives into their strategic and business plans. Take the first steps in the certification process by
scheduling your free assessment today!
MEET OUR EXPERT: Andy Nichols, Program Manager
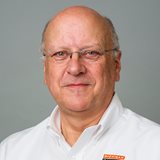
To The Center’s clients, Andy Nichols, CQP FCQI, brings 40 years of expertise in a wide variety of roles and industries, with a particular focus on quality management systems in manufacturing organizations. Prior to joining the Michigan Manufacturing Technology Center, he was the East Coast Regional Sales Manager for NQA, a “Top 5” Global Certification Body, responsible for significant sales growth in a highly competitive marketplace. He has authored three books, “Exploding the Myths Surrounding ISO 9000 – A Practical Implementation Guide” (published by ITG in April 2013) and “A Guide to Effective Internal Management Systems Audits" (published May 2014) and “Implementing ISO 9001:2015 – A practical guide to busting myths surrounding quality management systems” (published October 2022).
Since 1991, the Michigan Manufacturing Technology Center has assisted Michigan’s small and medium-sized businesses to successfully compete and grow. Through personalized services designed to meet the needs of clients, we develop more effective business leaders, drive product and process innovation, promote company-wide operational excellence and foster creative strategies for business growth and greater profitability. Find us at www.the-center.org.
Categories: Quality Management