6/17/2022
BY: ANDY NICHOLS
In manufacturing, we must measure or test the products we make because there is variation in the results and we don’t want to exceed the specification which would result in additional costs, time lost and possibly customer dissatisfaction.
Did you know the act of measuring the products we manufacture also has variation in it? There are several sources of variation, just as there are with manufacturing processes, and it's worthwhile spending time to understand them. After all, nobody wants to scrap thousands of dollars of product because a measurement result was wrong.
UNDERSTANDING THE VARIATION
If we use an Ishikawa Diagram (aka Fishbone), we can see that variation is caused by:
-
Man – usually discovered through using a Gauge R & R
-
Method – also usually discovered through a Gauge R & R
-
Material – we will omit this for the moment
-
Machine –the measuring equipment
So, how do we know how much variation is inherent in the equipment that is measuring the products? Studying the variation is called “calibration,” and it can tell us how the equipment functions over time. Unlike when an item of equipment is simply “verified,” the science of calibration evaluates the amount of variation present compared to a finite value by using mathematical methods.
We can now use the diagram shown above when considering the process of calibration, and we will see the same things affect the variation found because it is another measurement. This time it’s being performed on the measuring equipment, not on the product being made. Typically, an organization sends some of its measuring equipment to a calibration service supplier (a laboratory) and it’s common for the lab to be accredited (ISO/IEC 17025). The accreditation attests that the lab understands the variation inherent in the calibration processes. They include the equipment used to calibrate the lab’s equipment, their personnel, the environment under which the calibration was performed and so on. In the lab’s mathematical analysis, they consider the amount of variation in two categories known as “uncertainties.”
Since the lab cannot be 100% confident of measuring an exact value (due to various influences), they report their results based on knowing and assigning a mathematical value (known as “Type A” uncertainties and an estimate of the others, known as “Type B” uncertainties). This mathematically derived value allows the lab to report the results of their calibrations with a degree of confidence – indicated with a “k” and usually the digits 2 or 3. These equate to the standard deviation, “Sigma” (σ), and describe the level of confidence in the reported accuracy. For example: k = 2 being 95% and k = 3 being 99%.
WHY IS THIS IMPORTANT?
The lab’s results should be used to guide the next planned recall and calibration of the equipment by your organization. After all, annual calibrations commonly performed on measuring equipment do not consider the amount of use it’s had in that period. What would happen if the organization added a second or third production shift making parts? Now the equipment is being used at a much higher rate, so the recall should be shortened. Without knowing where in the tolerance band the measuring equipment is performing, we cannot set a recall point and remain within the operating limits with confidence of catching it before it goes out of specification.
Careful use of calibration services, and the results obtained, can benefit the organization:
WHAT DOES VERIFICATION DO FOR US?
It’s a word which is frequently - and somewhat incorrectly - used interchangeably with the term “calibration.” It’s quite usual for operators to perform a verification of their measuring equipment (micrometers, vernier calipers etc.) before use, usually against a calibrated “master” device, like gauge blocks. Doing this provides them with some instant feedback that the device hasn’t been damaged or worn before they use it. It’s a useful “health check” of the device and doesn’t involve the math associated with the act of calibration.
MEET OUR EXPERT: Andy Nichols, Program Manager
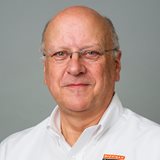
To The Center’s clients, Andy Nichols, CQP MCQI, brings 40 years of expertise in a wide variety of roles and industries, with a particular focus on quality management systems in manufacturing organizations. Prior to joining the Michigan Manufacturing Technology Center, he was the East Coast Regional Sales Manager for NQA, a “Top 5” Global Certification Body, responsible for significant sales growth in a highly competitive marketplace. He has authored two books, “Exploding the Myths Surrounding ISO 9000 – A Practical Implementation Guide” (published by ITG in April 2013) and “A Guide to Effective Internal Management Systems Audits" (published May 2014).
Since 1991, the Michigan Manufacturing Technology Center has assisted Michigan’s small and medium-sized businesses to successfully compete and grow. Through personalized services designed to meet the needs of clients, we develop more effective business leaders, drive product and process innovation, promote company-wide operational excellence and foster creative strategies for business growth and greater profitability. Find us at www.the-center.org.
Categories: Manufacturing,
Quality Management