6/1/2018
BY: ANDY NICHOLS
An important requirement of ISO 9001 (and its “cousins,” AS9100 and IATF 16949) deals with internal quality management audits. One purpose of this internal audit program is to look at the processes within the quality management system. Common questions that internal auditors raise during this practice include, “How do I audit a process?” “Which processes should I start with?” and “How will I know if the process is effective?”
Starting at a very basic level, a process can be defined as “activities that transform inputs into outputs.” One might add to this definition that the activities occur “under controlled conditions,” since we usually prefer to be able to predict a (good) result or output! From this definition, we know a number of things already about any process, including that they have:
- Input(s)
- Output(s)
- Activities
- Controls
This is helpful to start with, but heading off to do an internal audit with only four topics on a checklist is unlikely to help us reveal if a process is working as intended. Auditors must build from this list by developing a better understanding of what is needed for a process to deliver a satisfactory outcome - for both the organization and its customers.
Most business processes have some form of goal or objective assigned to them, which can be focused externally on customers’ needs or internally to the organization. These goals make it so that performance and success can be more effectively measured. If the process is working effectively, it’s by this performance criteria that an auditor can tell what is being achieved.
In addition, it’s desirable to produce a consistent result; therefore, the process must be under control. Most of us know the wailing sound (output) a loudspeaker makes when a microphone (input) is placed too close to it – that’s called feedback! You can certainly measure the sound level using this practice, but the process is out of control! Our business processes need controls to ensure that things don’t get out of hand.
Process controls may be accomplished in many ways, including:
- People – competent, aware and trained
- Equipment – capable and maintained (calibrated, if necessary)
- Methods – procedures and work instructions (as necessary, under document control)
- Materials – approved, available, identified, etc.
In listing these controls, our gathering of audit topics has grown quickly – but it’s not finished yet. We must also consider some other necessary controls, including documentation controls, non-conformance, records generated from the process, corrective/preventive actions and improvements.
The challenge with preparing for any audit is figuring out the sequence in which to place these so that we can gather useful information about the process, rather than just compliance-based facts. After all, arriving at a machining cell and asking for records of maintenance before you have established what product is being made, how many, and so on, will not reveal much useful information.
To make this process of planning an approach easier for auditors, a number of visual metaphors have been developed. One unique approach that has proven successful in helping auditors to organize these topics into an appropriate sequence – or “game plan” – is called the ‘Football©’.
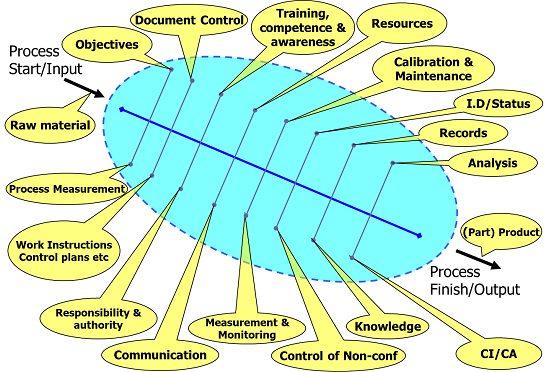
Using this football-shaped tool to ‘visualize’ the path an internal auditor should take when auditing has a number of advantages:
- More comprehensive planning so that all relevant controls are considered, and in their correct sequence. The above example can be easily applied to a manufacturing process. It also can be tailored to fit the structure of audit checklists or questions. This allows information to be gathered and used later to verify performance. This football diagram can assist an audit manager with ensuring the assigned auditor(s) do the relevant research of those requirements and controls so that they develop a better understanding of them before the audit interviews begin. The auditor then has a ‘bigger picture’ to audit and is therefore more likely to identify systematic issues.
- Better equipped to evaluate the results of the process when compared to what was planned to happen (not just the transformation of inputs). Auditors are then able to identify places within (or supporting) the process that could cause the plan not to be achieved (scrap, rework, downtime, etc.).
- Better time management through adherence to audit scope, etc. By populating the various ‘bubbles’ (in the example above) with the details of the organization’s management system and/or customer requirements, etc., the auditor is able to get a clearer understanding of the expected outcomes. They are then more capable of identifying where supporting processes are effective, without having to follow multiple “trails.” It is often easy for an internal auditor to be ‘drawn off track’ when evaluating these other criteria and controls (depicted by the football’s laces) that can affect a process – calibration and training, for example. The football can assist auditors in defining the ‘boundaries’ at which point they must decide to return to the normal process flow.
Conducting process-based internal quality management system audits can be an overwhelming task for many auditors. As a result, it is common to have compliance only-based reports (“we did/didn’t follow procedures”) instead of confirming effectiveness of the process. The use of a planning tool like the football to map out an auditing strategy leads to far more effective – and efficient – audits and helps the auditor focus on validating the results of the process to the goal.
Learn more about how to use the football diagram when planning for any process-based QMS audit at The Center's upcoming free Explore event on June 26 from 8:30am-10:30am.
MEET OUR EXPERT
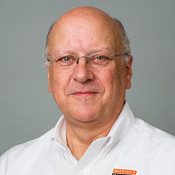
Andy Nichols, Quality Program Manager
Andy has 40 years of expertise in a wide variety of roles and industries, with a focus on quality management systems in manufacturing organizations. In addition to his ISO 9000 Management Systems experience, he has worked extensively with ISO/TS16949, ISO/IEC 17024 and ISO/IEC 17025. His broad practical knowledge of ‘Quality Tools’ includes: SPC, FMEA, Quality Circles, Problem Solving, Internal Auditing and Process Mapping. He also has been an IRCA and RABQSA accredited Lead Auditor.
Since 1991, the Michigan Manufacturing Technology Center has assisted Michigan’s small and medium-sized businesses to successfully compete and grow. Through personalized services designed to meet the needs of clients, we develop more effective business leaders, drive product and process innovation, promote company-wide operational excellence and foster creative strategies for business growth and greater profitability. Find us at www.the-center.org.
Categories: Quality Management