6/17/2016
A kamishibai board is a visual control center in the workplace used for performing audits within a manufacturing process. A series of cards are placed on a board. Green side out means the team has preformed the task and all is well. When the red side faces out, it means attention is needed or the task has not yet been completed. This ensures the safety and cleanliness of the workplace is maintained and that quality checks are being performed.
Quality must be built in to each process, making sure each person checks and is resposible for their own work. But this is not enough to guarantee 100% quality. It is a myth to think that “lean means no inspection”. In fact, there are multiple checkpoints – and checks of checkpoints - within a build-in-quality system.
What It Does
Kamishibai is an example of extensive process checks and standards. It:
- Ensures safety and cleanliness of the workplace are being maintained and quality checks are being performed.
- Promotes ‘Let’s Go See Management’ walks using a structured format for our leadership in performing day to day audits.
- Formalizes, prioritizes and schedules the checks to be made in the work place.
Day-by-Hour-by-Hour Boards, Andon Lights, and Kamishibai Boards are all visual management tools that facilitate the ‘Let’s Go See Management’ walks. These visual management tools are used in shift-to-shift communication meetings to promote a workplace-focused lean management culture.
The kamishibai board is particularily useful when there is a will and a desire for managers to practice Let’s Go See Management Walks but who are unsure of how to structure, or even what to do, when they are on the shop floor. The kamishibai system formalizes, prioritizes, and schedules checks to be made in the work place. It is a simple and flexible visual tool to ensure the required checks are being completed.
Why Do We Need A Kamishibai?
The main goal of Kamishibai is not to catch people doing something wrong. The proper use of a kamishibai is to train your eyes to see problems (deviations from the standard), identify improvements while they are still small, and teach others to see and solve these problems.
In the kamishibai system, faithfully completing the audits is as important as the result of the audit itself. The purpose is not to find faults, although problems should certainly be made visible. The purpose is to get in the habit of checking each day.
The Kamishibai card is printed on both sides with one side green and and one red side. To minimize problems with individuals and who may be color blind, a symbol should be added to identify go (O) and no-go (X) conditions.
See An Example
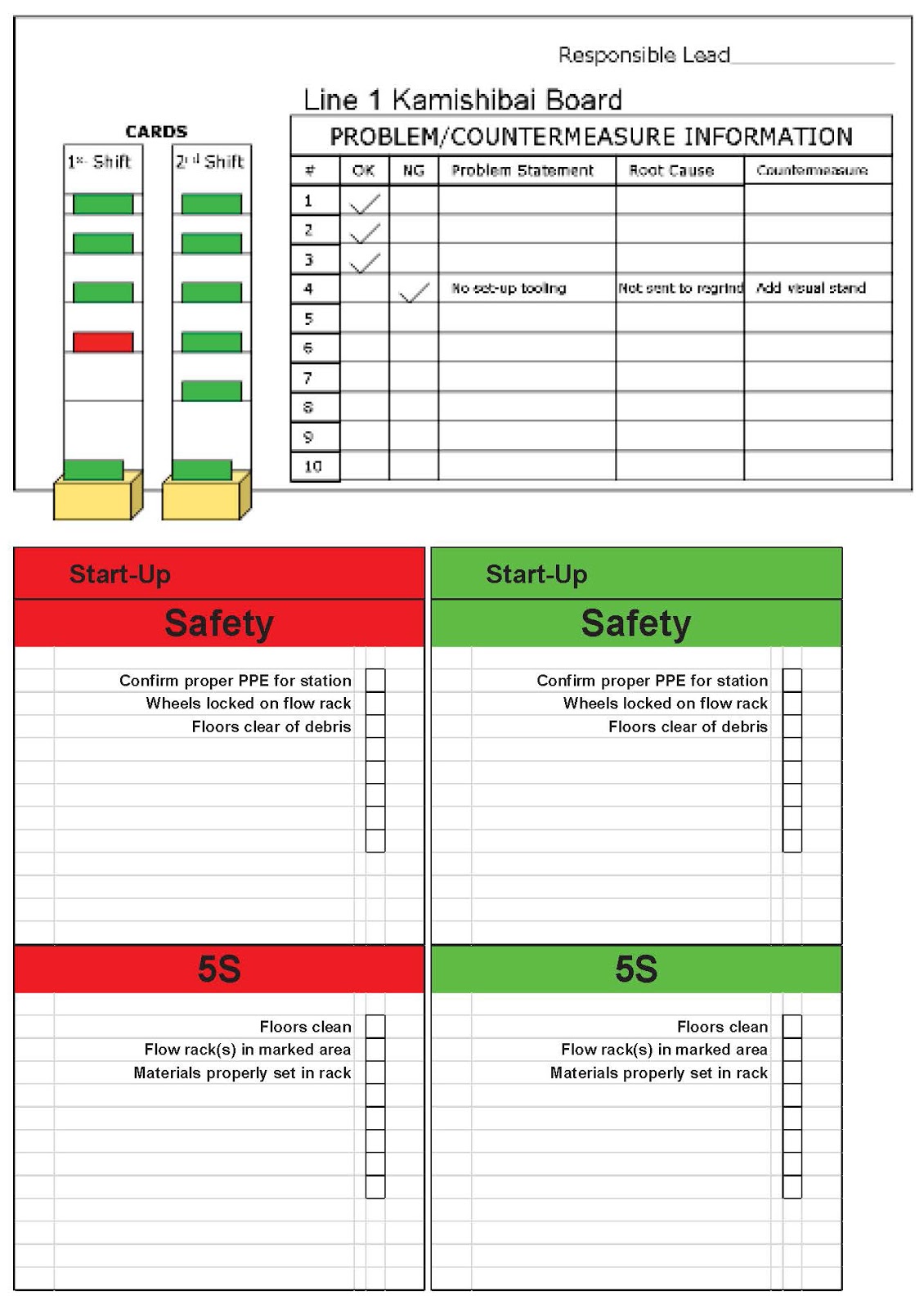
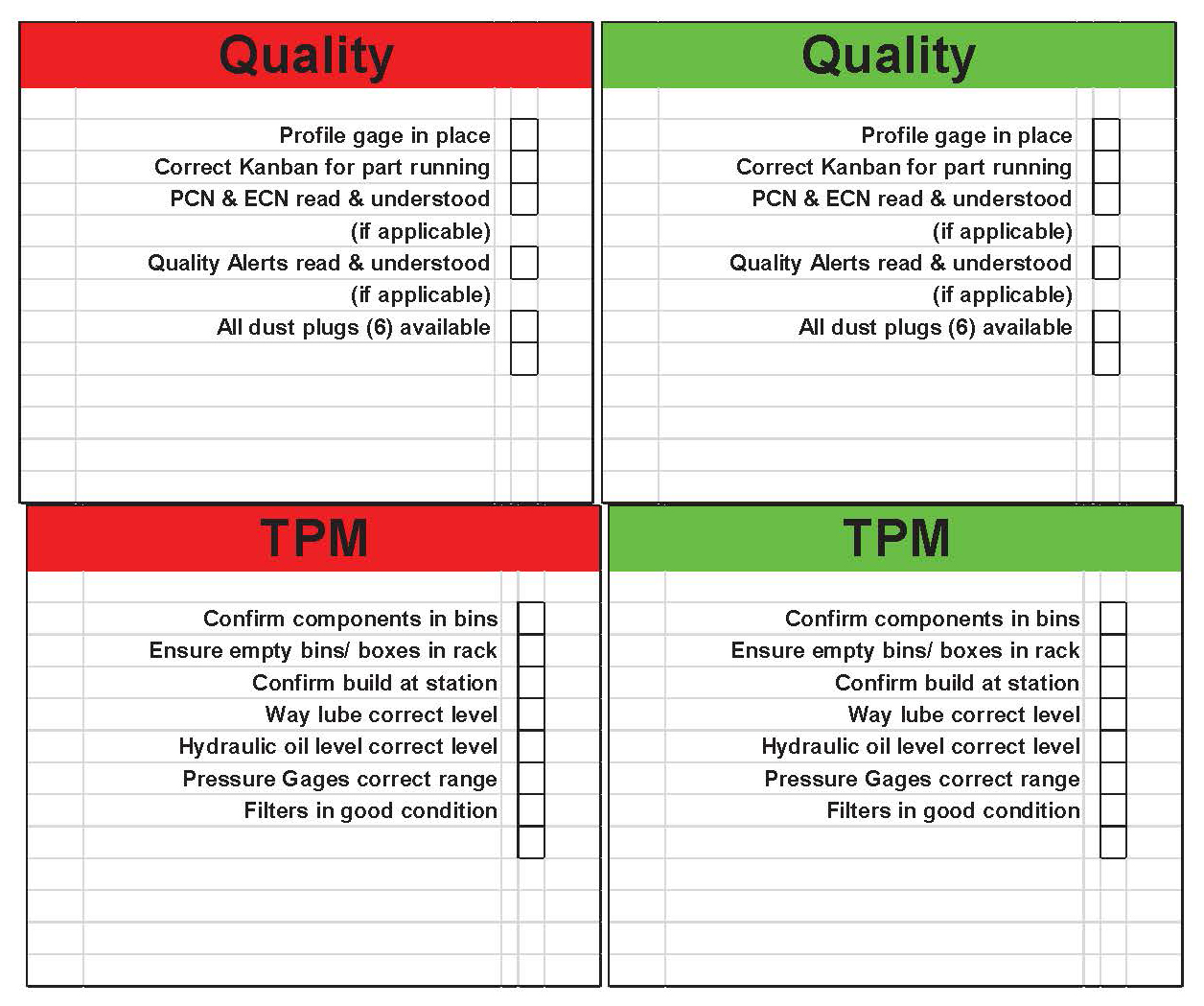
Learn more about how to create a lean enterprise using these tools by contacting the Michigan Manufacturing Technology Center. We offer a variety of Lean Business Solutions. For more information, call 888.414.6682, visit
www.mmtc.org or email inquiry@mmtc.org.
Since 1991, the Michigan Manufacturing Technology Center has assisted Michigan’s small and medium-sized businesses to successfully compete and grow. Through personalized services fitted to meet the needs of clients, we develop more effective business leaders, drive product and process innovation, promote company-wide operational excellence and foster creative strategies for business growth and greater profitability. Find us at www.mmtc.org.
Categories: Lean Principles