What if I told you I recently had a conversation with a company who decided it wasn’t worth the cost of implementing Lean in their facility? They believed their employees did not have time for training and the overall investment, including temporary loss of production, was too expensive. This company believed it would cost too much to dedicate 10 minutes of clean-up time at the end of their shift. Sounds crazy, right? However, many companies think this way when they don’t fully understand Lean manufacturing and its benefits.
IMPROVE PROCESSES WITH LEAN
Often, when we think of making changes, we want to attach it to a dollar figure. What can we do to save money here or there? However, it is not as easy to find that amount when looking at hidden costs such as non-utilized talent or time spent moving around the facility.
Although every company is different, it’s safe to assume that everyone experiences some type of cost that could, and should be, eliminated from the process. In the spirit of Lean, we call these costs waste. The main purpose of Lean improvement is to remove the non-value-added wastes affecting the process and make changes to improve quality and efficiency. Moving forward with Lean improvements means you are on the path to being a world-class organization leading your industry.
It is not necessary to tie every improvement to some type of tangible savings to justify doing it. Do you often look at data related to lost productivity based on time spent looking for things? Probably not.
POSITIVELY IMPACTING MORE THAN ROI
Let’s look at the foundational 5S practice, which is comprised of Sort, Set in order, Shine, Standardize and Sustain. By completing each phase, we can make an area clean, safe and organized. A cleaner, more organized workplace will eliminate extra time spent looking for tools, reduce accidents, improve quality and free up valuable space. However, it can be difficult to capture the return on investment (ROI) for 5S.
Once you have worked through 5S, compare the before and after. Can you tell the process is better by observing the area? Did attitudes and overall employee performance improve? Were safety hazards removed? Hopefully your answers are yes, and you can see the benefits of doing this throughout other areas in your facility.
It may be tempting to justify each Lean improvement by comparing the costs with savings. But making improvements without always having this comparison will still set you on the path to becoming the best in your industry on cost, quality and efficiency.
GET LEAN WITH THE CENTER
Our Lean manufacturing experts want to help your company discover ways to improve your processes. Lean training services at The Center will provide your company with the necessary tools to eliminate waste and strengthen processes for today and the future.
Learn more about how we can help and start training today by
registering for an upcoming course.
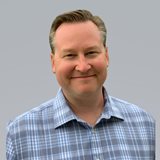
Jered Tyack is a Lean Program Manager at The Center. In his role, Jered provides custom training and mentoring to Michigan manufacturers on Lean principles and tools, helping them to reduce waste, increase efficiency and improve workplace culture. His areas of expertise include continuous improvement, Lean, efficiency and organization. Drawing from his wealth of experience and passion for continuous improvement, Jered guides manufacturers through their strategic improvement projects.