7/10/2015
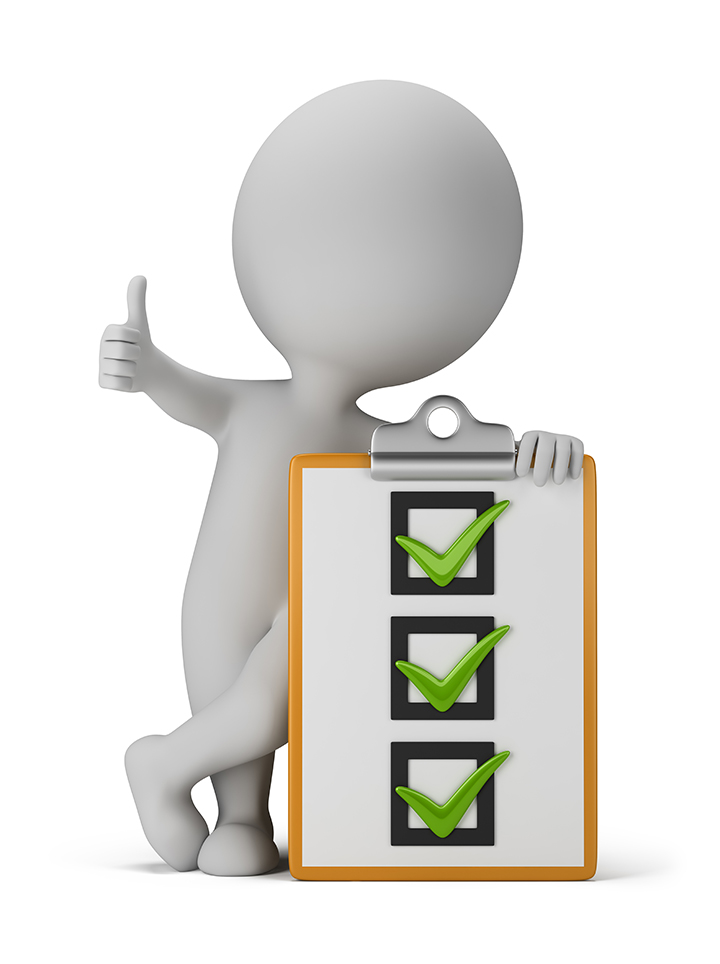
All manufacturers want to boost productivity and efficiency while reducing errors and accidents. Standardization of work, which can be difficult to adopt initially, can be an effective way to increase productivity and efficiency since it defines expectations, formalizes processes and creates accountability. Not all employees may welcome standardization initially, since it is perceived to reduce opportunities for creativity and individual decision-making, but when executed correctly and with professional assistance, the benefits to the company and staff are great.
What is Standardized Work?
Standardized work is a detailed, documented and visual system where staff develop and follow a predefined series of steps. The detailed process of steps, which we call standardized work, represents the current best practices for workers to follow in order to complete their defined task. They are designed to minimize process variation introduced by the worker and to eliminate unnecessary motion, ultimately reducing waste, easing problem solving and enhancing productivity.
It is also important to note that standardized work provides the baseline required for continuous improvement. Without it, continuous improvement activities are unmanageable because processes are constantly changing. The same job may be performed by different individuals-each accomplishing their task in a different way with no record as to how they did it. Detailed understanding of the steps needed to be taken to complete tasks is necessary to eliminate root causes and permanently resolve issues.
Reap the Benefits
Some of the benefits of standardized work include:
- Employee involvement and empowerment (when executed appropriately)
- Consistent processes for different employees to follow
- Optimizes staff training and new employee orientation
- Employee safety is highlighted and a top priority
- Improved productivity
- Increases customer satisfaction
- Improved, consistent quality
- Shifts blame for errors from the worker to the system
- Reduction/elimination of errors and mistakes
- Makes management responsive to employee needs
- Makes for much easier problem solving
Understanding the Goal
It is important to realize that standardizing work for the sake of standardization is not the ultimate goal. In a Lean organization, standardized work goals should aim to achieve greater safety, quality, cost control, and EMPLOYEE MORALE. From production floor workers to warehousing teams, allow your staff to contribute their thoughts as to what works and what doesn’t. Always ask yourself: Why are we doing this? Don’t bark out orders. Unquestioned compliance rarely works with children, yet alone adults.
MMTC Can Help
By adopting Lean practices, such as standardized work, you have an opportunity to achieve a better trained, productive and efficient workforce. When executed with the assistance of quality, expert professionals-like the kind at MMTC-standardized work can make a significant, positive difference. To help you gain the full benefits of Lean Business Solutions, MMTC conducts an assessment of your facility and manufacturing processes-working with your executive team to develop a roadmap for implementing profitable, positive solutions for your company. Call 888.414.6682 to speak to an MMTC Lean Expert or click here.
Since 1991, MMTC has assisted Michigan’s small and medium-sized businesses compete and grow. Through personalized services fitted to meet the needs of clients, we develop more effective business leaders, drive product and process innovation, promote company-wide operational excellence and foster creative strategies for business growth and greater profitability. Find us at www.mmtc.org.
Categories: Lean Principles