1/13/2023
BY: ANTHONY WELSH
It wasn’t until after a decade of working as a mechanical engineer that I really understood the crucial concept of letting the questions lead. While working on discovery-based projects, we must spend ample time documenting our question(s) before jumping into action. Albert Einstein was quoted as saying, “If I had an hour to solve a problem, I’d spend fifty-five minutes thinking about the problem and five minutes thinking about solutions.” Consider the fact that the smartest person in the room might not be the one with all the answers, but the one with the right questions.
QUESTIONS LEAD, ANSWERS FOLLOW
Our initial questions are about what defines a project. In the Six Sigma classes I teach at The Center, I can often be heard quoting the phrase, “Questions lead, answers follow.” This simply means you cannot determine what actions to take until you know what questions you are trying to answer.
The questions we have should influence what type of data-gathering study we design and execute, or the method by which we perform an investigation. I’ve seen OpEx practitioners jump to implementing a certain tool, or managers asking engineers to utilize a large dataset before they’ve defined the goals of the project. This is how projects end up late and over budget.
WHY SHOULD QUESTIONS LEAD?
If you don’t like the answers you are getting, you probably need to change the question. The questions we ask generate paths of discovery for the project. Therefore, questions not asked will be paths not explored. On top of this, progress can be slowed due to ambiguity, differences of opinions, agendas, indecision, less important tasks, etc. However, once the question is stated, an appropriate tool is easily identified and we’re off to the races.
If you’ve ever experienced what I call ‘analysis paralysis’, maybe it’s because you don’t fully understand what questions you’re trying to answer. We can end up sprawling with indecisiveness if given no constraints for comparison.
If that’s not bad enough, imagine this in a team setting. As the number of individuals increases, the likelihood we’re all headed in the same direction diminishes if we haven’t previously identified the questions we’re all trying to answer. We’ll look back after two or three months and realize we’ve either missed some things, overlapped some efforts, or wasted time.
MAKE A VISUAL THOUGHT PROCESS
A simple tool can provide a method for organizing our questions and keeping the team on track. A thought map (TMAP) is a visual board that can be created in person or collaboratively online. Using this board, the knowledge gaps can be identified, and actions can be taken or delegated. This also becomes a communication tool as project progress gets documented and the knowledge gaps are closed. Once finished, the thought map records the full journey of the project and can be a reference for future projects.
There are six categories of information we want to include on a thought map: questions, theories, actions, information, predictions and results. To begin, a discovery-based goal is listed at the top, and questions or theories are listed horizontally. Content is then added to the map as new information becomes available.
There are many benefits to using thought maps. As you’ve seen by now, they encourage the asking of new questions, but they also:
-
Organize the teams’ thought process
-
Promote questioning both broadly and deeply
-
Provide focus and direction for next actions
-
Develop priorities among multiple tasks
-
Encourage parallel paths of work (don’t develop only one solution!)
-
Document the project for communication with others
Below is a simple example, but due to this article format, it’s just a small slice of what a full thought map might look like. Use software like Excel, Visio, Lucidchart or Google Sheets so you have room to expand both horizontally and vertically. I encourage you to try one out and see if it works for you. I know it’s been helpful for myself and my peers.
SIX SIGMA AT THE CENTER
If you’d like more detail, join us at The Center for a Six Sigma Green Belt or Black Belt class where we explore this technique along with a full methodology for solving our tough problems. Register for an upcoming course
here.
MEET OUR EXPERT:
Anthony Welsh, Six Sigma Master Black Belt
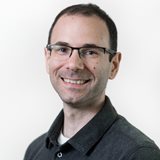
Anthony Welsh is a Six Sigma Master Black Belt with 20 years of experience delivering projects to both the automotive and consumer products industries. In his role at The Center, Anthony shares expert tools in critical thinking and data-driven decision-making to assist clients with using Six Sigma methods to achieve real results.
Since 1991, the Michigan Manufacturing Technology Center has assisted Michigan’s small and medium-sized businesses to successfully compete and grow. Through personalized services designed to meet the needs of clients, we develop more effective business leaders, drive product and process innovation, promote company-wide operational excellence and foster creative strategies for business growth and greater profitability. Find us at www.the-center.org.
Categories: Continuous Improvement,
Lean Principles,
Six Sigma