1/15/2016
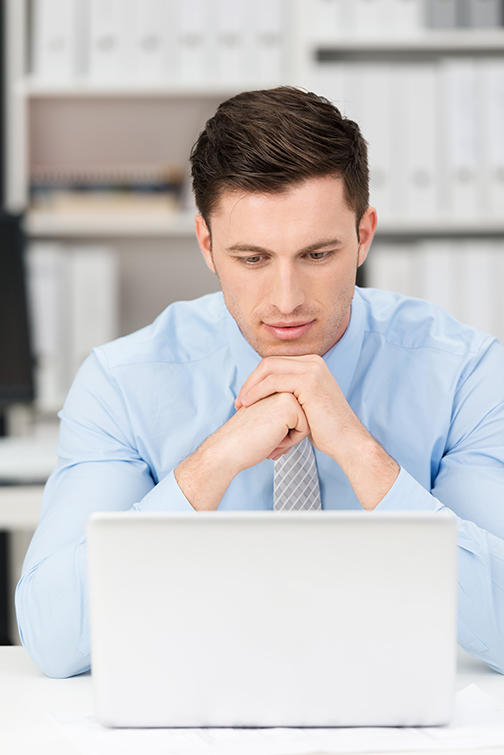
It isn’t uncommon for newly graduated and well-educated engineers to immediately begin their career in manufacturing. They sit down at a new desk, organize materials, and layout their “task” list provided by their new managers. Typically, the list includes the five things the manager would have accomplished when they held that job (had they known how), three things that have been “on the plate” forever and never accomplished, and one or two items that upper management believes should be a part of this year’s progress.
The Downsides of Lists
The trouble with the new job task lists is very simple:
- Often, the manager doesn’t understand why the five items ended up as tasks or know how to start correcting them (or he/she would have done that when they had the responsibility).
- The items that have been perennial tasks and never accomplished lack relevance (or the lack of completion would have prevented production).
- The lack of proper policy deployment (whatever that is) makes the “key objectives” too strategic to be approached at a tactical level.
Now What?
So the first question arising from this situation is ‘What do I do now’? A simplified answer: Be career conscious. One can’t ignore the tasks provided by superiors and expect career success. Develop a plan addressing the five items the manager wants accomplished, an incremental plan to make progress on the three perennial items, and finally, a list of questions regarding the key objectives. These questions will allow you to isolate what the objectives mean to you personally in order for you to determine the best path to show progress while staying within your own “sandbox”. To ignore any of them is career suicide. Unless you have an opportunity into a new, entrepreneurial career, they must be addressed in some meaningful way. That said, these are not always the best areas to spend most of your time to make real, meaningful progress in your new area. For instance, what if there are production issues affecting the line or product quality?
You will need to consider alternative priorities that will lead to real improvement.
First Things First…Research!
In your journey towards progress, research should be the first path you travel. Certainly, it isn’t advised you study a situation to death (paralysis by analysis), but you should learn the real underlying issues in your new area. There are three areas to begin your research in order of importance:
1. Production line stoppages and associated inefficiencies.
- Production line stoppages or pressing production requirements can and should take an immediate priority. Inefficiencies can be difficult to detect. There may or may not be a detection/audit process in place to determine if they are happening or whether they have an associated cause. If the information doesn’t currently exist, the first order of business is to set up a data collection system to track the shutdowns and/or stoppages. Before getting too involved, find out who is responsible for maintenance. They may already be tracking downtime in some fashion.
This downtime tracking should also be Pareto’ed, but the following sample layout could be used to collect the data if you don’t already have something:
2. Customer rejects and customer feedback (not always the same thing).
- When reviewing customer rejects, keep in mind they can be formal or informal. Formal rejects will include something documented electronically, on a website for example, or printed. Nearly every customer has one or the other, so they exist to be found. The number of pieces rejected and customer cause should be Pareto’ed, or bar charted. (CHECK BACK FOR OUR BLOG HIGHLIGHTING PARETO ON FEB. 12)
3. Any warranty claims associated with the product produced.
- Warranty should be investigated based first and foremost on what the costs are. You’ll need a copy of the contract for the parts to determine liability. Secondly, you’ll need to view the occurrence level or how often a failed part is detected.
To request a copy of the above Excel document, which includes the formulas which add the times per day and the totals per individual problem, or if you have any questions, contact Bob Jenkins at
bjenkins@mmtc.org. Start documenting your data now and you’ll have a month’s worth to analyze before the follow up blog on Feb. 12 is posted.
Since 1991, MMTC has assisted Michigan’s small and medium-sized businesses compete and grow. Through personalized services fitted to meet the needs of clients, we develop more effective business leaders, drive product and process innovation, promote company-wide operational excellence and foster creative strategies for business growth and greater profitability. Find us at www.mmtc.org.
Categories: Leadership/Culture,
Quality Management,
workforce