2/10/2023
BY: BOB JENKINS
In my
last blog, we discussed the importance of being a proficient problem solver in your quality role. So, after learning the problem-solving process and exercising it to effectiveness, stop and ask yourself, “What else makes me the most effective in my role?” That’s an easy one…
UNDERSTANDING VARIATION
Statistical Process Control (SPC) is a cornerstone of making the manufacturing process both effective and efficient. SPC teaches us how to characterize variation. Variation is what gives quality professionals work to do. If companies ran smoothly and had no variation, most of us wouldn’t need to go to work. Understanding the concept is vital to creating a product that satisfies customer requirements (effectiveness) and keeps us in business (efficiency).
The Toyota Production System from Japan was hailed as the savior of the U.S. auto industry when it implemented SPC in the 1970s. The SPC ideology was coined by Dr. Walter A. Shewhart from Bell Labs (the Apple of its time). Dr. Shewhart taught SPC to Dr. W. Edwards Deming who was drafted by the U.S. government to go to Japan and help revive manufacturing after WWII. To this day, the Deming Award is the most prized award in Japanese manufacturing.
I was lucky enough to attend a yearlong seminar series at Ford in which Deming, who was then about 78, laid to waste the thought that management was preeminent in making manufacturing successful.
THE SIMPLER, THE BETTER
In his seminar series, Dr. Deming maintained that management was responsible for 85% of process variation and problems that arise in manufacturing. He pointed out that SPC was a simple concept and suggested that Dr. Shewhart made SPC sound more complicated than it was.
At the Michigan Manufacturing Technology Center (The Center), we have a way to make it simple again. In many cases, new
Industry 4.0 technologies can provide better ways to measure. However, understanding SPC can’t be replaced by computers. SPC is an essential skill for manufacturers to have under their belts to improve quality within the company.
Variation in all that we do is key, and The Center is here to help you learn how to apply it to make your business more effective and efficient. The Center also offers
Six Sigma Green, Yellow and Black belt training, which will lead participants to even more levels of understanding and overcoming variation.
MEET OUR EXPERT: Bob Jenkins, Quality Program Manager
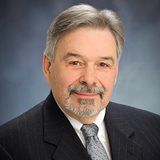
Bob Jenkins is a Quality Program Manager at The Center. In his role, he manages and delivers training and implementation assistance to organizations in the field of quality improvements. As an Exemplar Global Certified Auditor, Bob assists clients with Quality Management System implementations such as ISO 9001:2015 and IATF 16949. He provides internal auditor training and consulting services for various groups, including production, production management and corporate management, in disciplines involving the automotive core tools of quality systems consisting of FMEA, PPAP, APQP, SPC, MSA, and Root Cause Analysis/Problem Solving.
Since 1991, the Michigan Manufacturing Technology Center has assisted Michigan’s small and medium-sized businesses to successfully compete and grow. Through personalized services designed to meet the needs of clients, we develop more effective business leaders, drive product and process innovation, promote company-wide operational excellence and foster creative strategies for business growth and greater profitability. Find us at www.the-center.org.
Categories: Continuous Improvement,
Manufacturing,
Quality Management