2/26/2021
BY: PETE SCHMIDT
When I ask manufacturers about their biggest challenges, nearly all mention the lack of available skilled workers. With so many companies looking to hire, this added competition only further compounds the challenge.
In our most recent Smart Solutions Series webinar, we explored how Lean manufacturing principles can be applied to an organization to maximize productivity – effectively filling these critical gaps in production using existing resources and talent. A brief summary of our virtual discussion is outlined below. To view the webinar recording, click here.
MAKE THE MOST OUT OF YOUR WORKFORCE WITH LEAN
While most manufacturers are familiar with the concept of Lean manufacturing, not all have implemented the tools and principles into their practices. The main objective of Lean is to improve efficiency while eliminating waste. It’s important to note that Lean thinking does not consider only scrap and rework as waste. Lean believes there are eight different kinds of waste, which are Defects, Overproduction, Waiting, Non-Utilized Talent, Transportation, Inventory, Motion and Extra Processing. Once these types of waste have been minimized and efficiency has been improved, manufacturers can maximize the utilization of their current workforce, accomplishing more work using less resources.
The structure of Lean is often visualized using the House of Lean below. Like everything that you want to last, you must first start with a strong foundation, then build structures on top of that and protect it all with a roof.
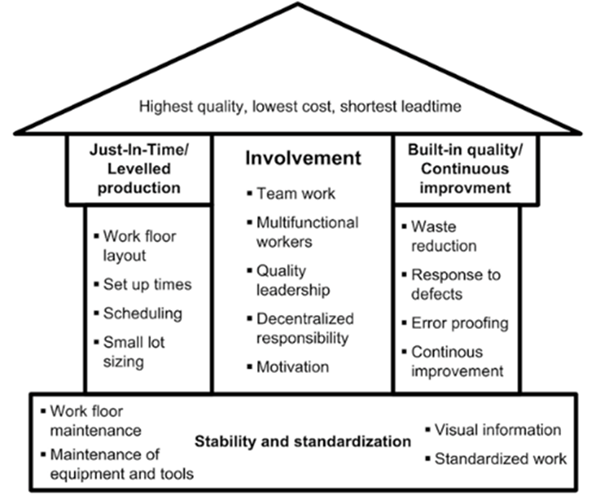
Establishing these principles, maintaining them and always striving for continuous improvement will lead to success both within the factory and in the office. The following real-world applications demonstrate how Lean tools can be used to achieve these goals.
- A seat frame manufacturer serving the automotive industry began a program for basic seat framing. As the customer added more features and volume, the manufacturer kept adding more bodies, only to fall farther and farther behind. They engaged The Center for both a Kaizen event and Value Stream Mapping to identify pain points within their production process. After enacting several small improvements, like minimizing movement waste and balancing the work along the line, the company realized massive improvements. Overtime decreased, cycle time decreased, and two workers were freed up to move to a different area in the plant.
- Another company that was successful with a Lean manufacturing implementation began by failing to meet on-time deliveries and having their equipment break down regularly. They started examining the problem through a Lean lens by identifying multiple opportunities for improvement in production. After discovering operators from each shift were making products differently, the team implemented standard work instructions which helped reduced manufacturing time for each product by 20%. Movement waste of raw material also was dramatically decreased, helping to streamline production and eliminate the need for overtime. As a result of this saved time, the maintenance team was able to conduct preventative maintenance for multiple hours each day to complete the necessary maintenance for their equipment. This nearly eliminated further equipment disruptions in the operations. With these Lean improvements in place, the company was able to maintain the same amount of output with the same amount of people, using much less time – leading to substantial financial savings.
Just as important as implementing Lean is making sure the improvements are sustained over time. Visual reminders must be placed around the plant floor so workers’ eyes are never taken off the process.
The journey towards improvement is never finished, as there are always more ways to improve and better utilize resources. With the help of Lean tools, manufacturers can successfully tackle some of their most significant problems – including the labor shortage.
If you are unsure of where to start with your Lean journey, The Center offers a free Opportunity Assessment that can look at your operations and give you a better idea of where to begin. Learn more at the-center.org or contact our Lean experts at inquiry@the-center.org.
For additional ways to solve your labor shortage, read a recap of our first Smart Solutions Series webinar about culture and stay tuned for our next webinar on March 17 from 9 - 10am where we’ll explore how technology can be applied to fill talent gaps.
MEET OUR EXPERT
Pete Schmidt, Business Solutions Manager
Pete Schmidt is a Business Solutions Manager at The Center. Operating directly out of Macomb County, Pete provides services and support to small manufacturers in the region to enable them to compete, grow and prosper. Prior to joining The Center, Pete spent more than five years at AXXO Sales, LLC, as Business Development Manager. There, Pete represented numerous companies and product offerings, helping customers manage business growth.
Since 1991, the Michigan Manufacturing Technology Center has assisted Michigan’s small and medium-sized businesses to successfully compete and grow. Through personalized services designed to meet the needs of clients, we develop more effective business leaders, drive product and process innovation, promote company-wide operational excellence and foster creative strategies for business growth and greater profitability. Find us at www.the-center.org.
Categories: Leadership/Culture,
Lean Principles,
workforce