2/8/2019
BY: MIKE BEELS
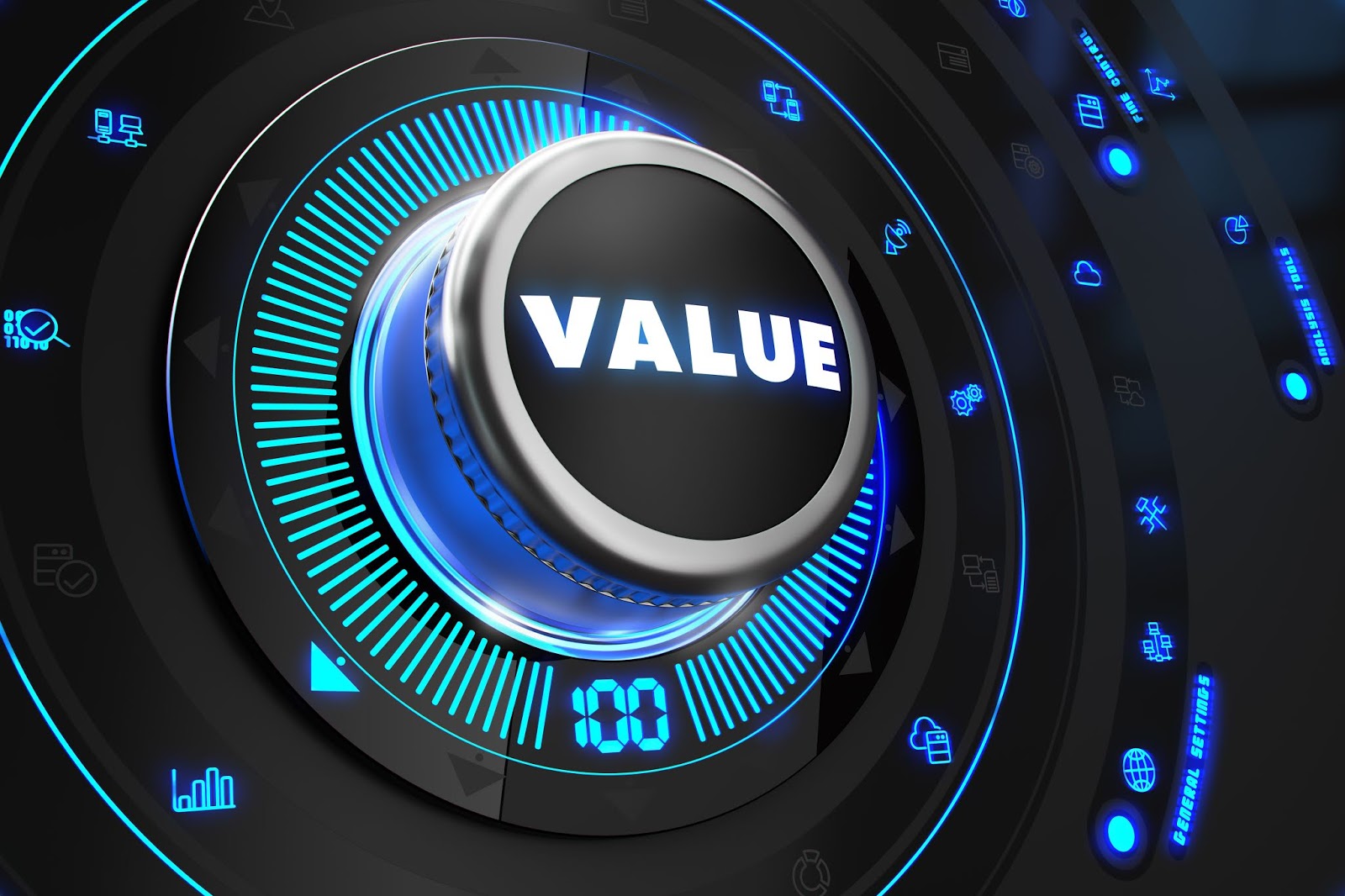
You’ve heard the old saying: Time is money. But how much of our time at work is really spent engaging in activities that add value to the organization? We tend to assume that every task we perform is essential in sustaining operations. But after analyzation from a Lean perspective, we might be surprised to discover that many of our activities are actually costing the organization time and money.
At its core, Lean is a methodology that aims to eliminate waste in all areas of an organization, resulting in shorter lead times, improved quality and reduced cost. One activity that Lean practitioners use to eliminate waste is to break down workplace processes into categories of Value Added, Non-Value Added and Necessary Non-Value Added. Completing this step allows manufacturers to identify which activities are actually necessary to satisfy the needs of customers, and which are simply wasting valuable resources. Once these distinctions have been made, manufacturers can then work to eliminate Non-Value Added activities so that waste can be minimized, while maximizing value added.
In order to separate your activities into these three categories, you must first understand what each entails:
Value Added Activities must satisfy the following three criteria:
- Work that the customer is willing to pay for
- Work that physically transforms the product (or document/information)
- Work that is done right the first time
One easy way to remember this definition is to use the acronym CPR, which stands for: Customer pays for it, Physically transforms the product, Right the first time.
Non-Value Added Activities involve work that consumes resources, but does not add value to the product or service.
Necessary Non-Value Added Activities are a bit trickier to identify. These are activities that do not add value to the product or service, but are currently necessary. For example, this work might be required by:
- Customer contract or specification
- Industry standard such as ISO 9001
- Government regulation
- Outdated work method or equipment
We now know what each of these categories involve, but what do they look like in daily life?
On the shop floor, Value Added Activities are those that transform the product from raw material into finished goods that the customer is willing to pay for. Examples might include drilling, piercing or welding a part. Non-Value Added activities, or those that consume valuable resources but do not meet the CPR criteria, might include extra motion or transportation involved in walking from one area of production to another, or any rework caused by defective products. Finally, if a customer requires you to maintain two weeks of finished goods because they don’t trust you to produce or deliver on time, this could be considered a Necessary but Non-Value Added activity. While the activity is Non-Value Added because it is creating extra inventory, it is Necessary because the customer expects it to be done in order to continue doing business with them.
These same types of Value Added, Non-Value Added and Necessary but Non-Value Added activities exist in the office as well. There, a Value Added activity might involve completing an accounting statement or drawing for the customer. On the other hand, a Non-Value Added activity could include the copying and filing of documents. To some, the need to utilize a corporate document at the plant level could be considered Necessary but Non-Value Added because although it may create additional work, it must be done.
Analyzing all the process steps involved in your operations, no matter how big or small, can put your company on a path to saving money while boosting efficiency, increasing customer satisfaction and even heightening employee morale. All it takes is asking the question, Is my work adding value?
For those interested in learning more about the basics of Lean, The Center’s Manufacturing Skills Development (also known as Manufacturing Process Development) course provides participants with a foundational understanding of manufacturing concepts including Lean, quality, problem solving and culture. Register for the upcoming course on March 21-22 here. To learn more about how to start your Lean journey, click here or contact inquiry@the-center.org.
MEET OUR EXPERT
Mike Beels, Lean Program Manager
Mike Beels has served in the role of Lean Program Manager for the Lean Business Solutions Team at The Center for more than 12 years. Mike’s areas of expertise include Change Leadership, Workforce Engagement and Succession Planning, as well as the entire portfolio of Lean strategies and methodologies. He is a professional trainer and has the ability to command an audience and deliver the training message in a way that participants can understand in a clear, non-threatening manner. Mike always leaves trainees excited and ready to complete training transfer to the shop floor or office.
Since 1991, the Michigan Manufacturing Technology Center has assisted Michigan’s small and medium-sized businesses to successfully compete and grow. Through personalized services designed to meet the needs of clients, we develop more effective business leaders, drive product and process innovation, promote company-wide operational excellence and foster creative strategies for business growth and greater profitability. Find us at www.the-center.org.
Categories: Continuous Improvement,
Lean Principles