8/12/2016
A company’s supply chain is an integral component to success. Therefore, any disruption can be a major threat to business continuity, including delays in production and distribution, reduced revenue, and decreased market share. From earthquakes and tsunamis to hurricanes and tornadoes, all have shown just how far risk can extend. Since volatility isn’t disappearing, we need to identify the triggers of risk events, the importance of developing a plan to mitigate them when they do occur, and how to establish monitoring metrics and activities in order to be prepared for the inevitable.
Develop a Risk Management Plan
A Risk Management Plan is an essential element to operational efficiency. It is important for every organization to understand the financial impact of risk. This requires each company to be able to estimate the financial impact of a potential supply chain risk event from suppliers as well as internal risk events within their own processes.
Your risk management plan should include:
- A risk mitigation strategy
- A risk impact analysis tool
- What value do we have at risk
- A risk event reaction plan, monitoring trigger event to be monitored by who, when, how
Work Flow Process Mapping
Risk exists at every level of an organization. Work flow process mapping is a simple tool used to help understand the internal and external risks of an organization. All business processes have workflows. In its simplest definition, a process workflow is a series of activities necessary to complete a task. This information is needed to determine what the Total Cost of Ownership of purchased and manufactured components, assemblies and finished goods are.
Creating a current state process flow map will help you understand your company’s efficiency. The visualization of a process helps to locate risk and identify improvements, especially in cases where a process workflow may be interdependent on a separate process and collaboration between departments is required.
Process workflows need to be developed using input from employees, customers, suppliers, and all other stakeholders. Aligning users will eliminate the risk of a process improvement in one area leading to a delay/inefficiency in a separate area. Consider what influences the process inputs and outputs have both internally and externally. A simple line of communication can avoid quite a bit of issues.
Companies pursuing growth are continually trying to improve their business practices. Assimilating new technology into your business process flows can quickly antiquate old business practices. This requires current and future state business flows to be documented. The future state business process flow can be used to train and communicate with team members how and why the future state business process flow will improve our operations.
An Introduction to Risk Management
This is the perfect time to introduce the concept of risk management and how the process workflow gives the users insight into how we can improve our risk and reduce our total cost of ownership.
Example: Recently the Michigan Manufacturing Technology Center worked with a company to streamline their accounts payable process. The risk they were facing was exceeding their line of credit at a major big box hardware company. This was very important to the company because they had 32 branches throughout the country installing their products. It is less expensive for the installation branch manager to purchase needed supplies to install their products than to ship and stock all those supplies at each branch location.
Accounts Payable visited the Big Box Hardware Store website and downloaded from their Credit Center all unpaid invoices (Open Invoice). This replaced the need to print out every individual invoice from the Big Box Stores. The plan was to use Big Box’s spreadsheet from the Credit Center to replace the hard copy match of each individual invoice of the purchase order. This saved an average of 16 hours of printing per week of Accounts Payable staff time. Each invoice required 2-3 minutes to print-and the company averaged 400 invoices per week, with the potential up to 600. Auditors will still be able to do drill down verification price testing on demand. This ensured timely payment of invoices and prevent the credit limit from being exceeded. It also helped to eliminate the risk of the install branch managers not being able to purchase needed supplies to install their products at the customer’s location because the credit limit has been exceeded, risking customer satisfaction and top line revenue.
Gaining Clear Insight
Process workflows map out the critical points of each task and allow for process owners to identify required resources. The workflow map will help establish a task hierarchy, eliminating the risk of duplicated efforts. It also helps eliminate the risk of rework due to critical stakeholders receiving the information at the wrong stage in the process.
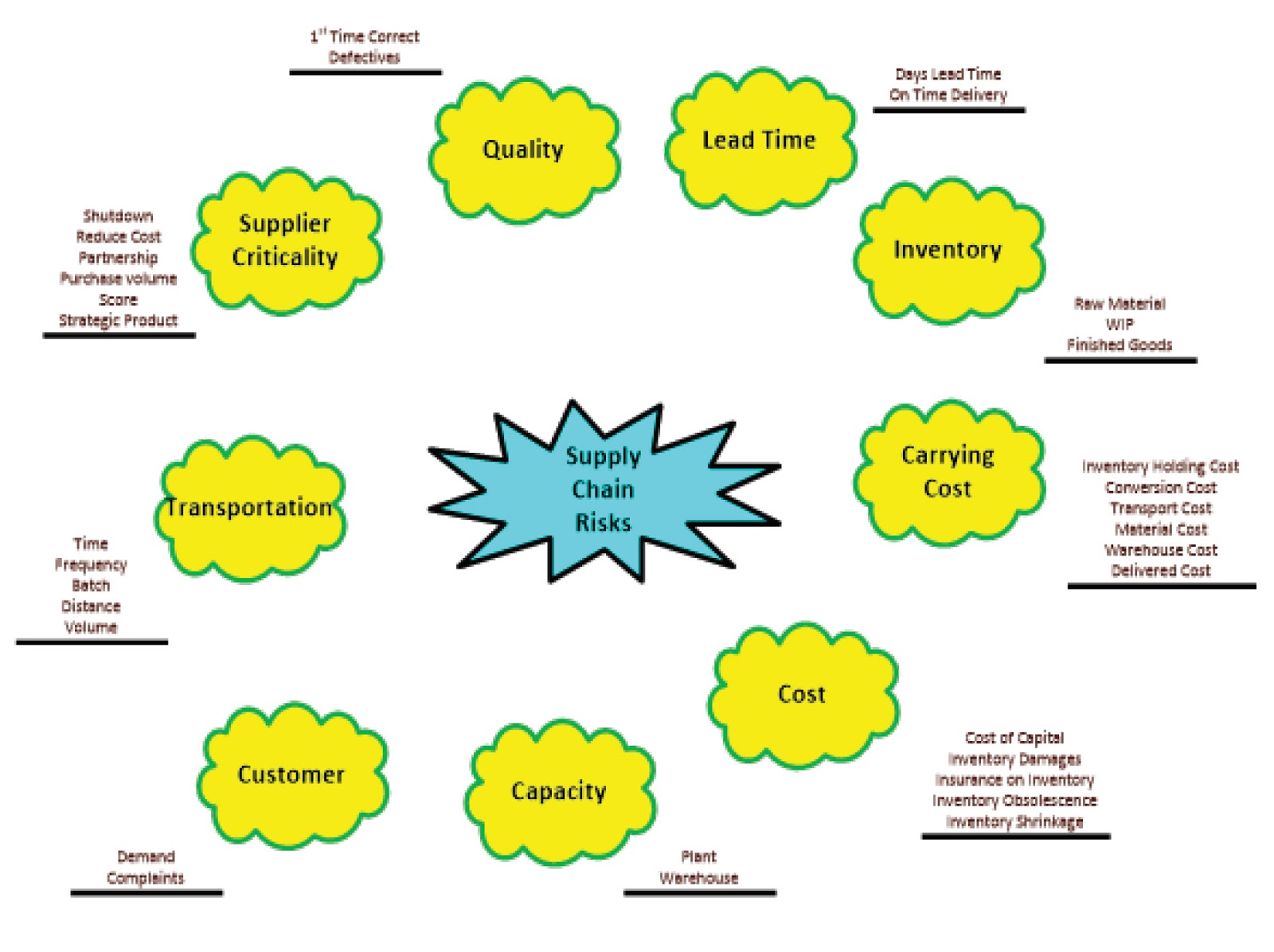
Often key stakeholders do not have clear insights into the ownership of specific tasks. These insights will bring security during times of employee turnover as there is less risk in processes being lost during the transition to a new team member taking ownership of a group of tasks.
Workflow analysis can be used to establish a clear path of escalation, drastically reducing downtime and eliminating the risk of confusion and delay. A lack of recognized ownership can halt a process because the team member does not know where to go for answers. Just as supplier workflow will provide you with insight into value adding processes, your customers may want insight into your workflow to help them when they are evaluating your business stability. It is also useful in locating areas of error, for any needed damage control and what future kaizen needs to planned and scheduled.
Process Workflows=Accountability
Defined process workflows hold each resource in a process accountable for their specific tasks. The ultimate result of a defined and agile process includes involved suppliers, accountable employees, and satisfied customers, which all fuel organizational growth.
Suppliers with inefficient processes or inadequate compliance may directly impact production and revenue targets. Suppliers with poor social responsibility practices may expose an organization to brand and legal risks.
Suppliers must be evaluated on quality management procedures, supplier corrective action request responses, documentation, requirements and specifications, testing, installation, change control, support and maintenance, security and electronic records compliance. Evaluation also includes review of potential legal, ethical and other potential regulatory issues.
Supplier audits are a necessary, time and cost prohibitive aspect of supply chain management. It is important a supplier be able to provide their customer current process workflows which provide:
- An in-depth risk assessments
- A tool to calculating the value that is at risks
- Understand their true Cost of Ownership to support and validate their decision-making
A good supply chain system not only allows one to rank the risk of their suppliers, but also identifies the suppliers who are prepared to improve their process. Suppliers who are actively working to reduce their risk, provide high quality products/services uninterrupted at the lowest cost. As a Good Supplier, we can combine workflow process mapping using risk management tools to proactively communicate to our customers that our organization is working to improve and reduce risk of an interruption in their supply chain.
Need supply chain assistance? Contact the Michigan Manufacturing Technology Center today at 888.414.6682 to discuss your needs.
About Us
Since 1991, the Michigan Manufacturing Technology Center has assisted Michigan’s small and medium-sized businesses successfully compete and grow. Through personalized services fitted to meet the needs of clients, we develop more effective business leaders, drive product and process innovation, promote company-wide operational excellence and foster creative strategies for business growth and greater profitability. Find us at on the web at www.mmtc.org.
Categories: Supply Chain