4/7/2023
BY: ANDY NICHOLS
ISO certification is often expected of manufacturers to ensure quality management is in place. Certification also gives companies a competitive advantage and the discipline needed for future growth. This discipline becomes evident in all aspects of the company by creating an environment ready to thrive in today’s competitive market.
When ISO certification is mentioned, many manufacturers first ask, “How much does it cost?” But that is not always the most important question to ask when embarking on a journey to certification.
After 30 years in the quality industry, I’ve gained a well-rounded understanding of the basics of the certification process. I’ll go into further detail of the whole process in my ongoing ISO Certification series. But for now, let’s stick to the basics with a David Letterman-style list of key aspects of certification.
10. Don’t select a registrar on price alone! (you may end up paying more!)
9. Don’t select a registrar based on being in the same state (the auditor may travel from out of state)
8. Certification is completed in two audits: “Stage 1” and “Stage 2”
7. You can request a specific auditor to conduct your audit
6. Beware of fees and always check the fine print in your certification agreement
5. The auditor isn’t always correct with their audit findings (you can appeal them)
4. The duration of your audit is based on publicly available information and is calculated from head count and scope (check out
https://tinyurl.com/bddbmp4u)
2. Certification is valid for three years, with annual “surveillance audits” (which are shorter in duration)
1. Your organization must have an operating, quality management system before you can be certified
In my next blog, we’ll take a deep dive into cost, outlining all you need to know before making any decisions.
ISO CERTIFICATION WITH THE CENTER
The experts at Michigan Manufacturing Technology Center (The Center) will guide you to ensure your company is ready for ISO certification. We can help you develop a quality management system (QMS) and ensure it is based on the necessary requirements.
Contact us today to get started.
QUALITY TRAINING AT THE CENTER
Audits can be daunting. Train a team of staff members who can help lead your company through an audit without the stress. Register for an upcoming Lead Internal Auditor class
here.
MEET OUR EXPERT: Andy Nichols, Program Manager
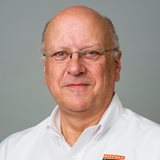
Andy Nichols, CQP FCQI brings 40 years of expertise in a wide variety of roles and industries, with a particular focus on management systems in manufacturing organizations. At The Center, Andy trains, consults and creates content covering many topics, including quality systems, information security, practical aspects of cybersecurity and business development. He has authored three books, “Exploding the Myths Surrounding ISO 9000 – A Practical Implementation Guide” (published by ITG, April 2013), “A Guide to Effective Internal Management Systems Audits (published May 2014) and “Implementing ISO 9001:2015 – A practical guide to busting myths surrounding quality management systems” (published October 2022).
Since 1991, the Michigan Manufacturing Technology Center has assisted Michigan’s small and medium-sized businesses to successfully compete and grow. Through personalized services designed to meet the needs of clients, we develop more effective business leaders, drive product and process innovation, promote company-wide operational excellence and foster creative strategies for business growth and greater profitability. Find us at www.the-center.org.
Categories: Quality Management