4/28/2023
BY: ANDY NICHOLS
Many organizations do a good job of satisfying their customers’ need for quality products and continue to meet the challenges of the markets they serve. Often, their (larger) customers have hinted at wanting their organization or supply chain to become “ISO certified” – for example, lower tier automotive suppliers are required to be ISO 9001 certified by higher tier customers. Some organizations may have seen their competitors are certified and question why. After all, doesn’t it cost a lot to be certified?
In part one of a three-part series, let’s look at ISO certification cost since it is critical to the decision-making process for any organization, particularly small ones. Before anyone starts obtaining quotes from ISO registrars (or certification bodies or conformity assessment bodies – depending on your market), there are some basic calculations you can do to estimate the cost of your own certification.
ESTIMATING COSTS
ISO registrars typically charge per day for their audits (8 hours) and experience shows this is $1,400 on average. The number of days each audit takes is defined in
publicly available documents which define some of the “rules” for registrars. On page 21, a table of audit days can be found and an estimate of costs to be certified can be figured.
For example, a CNC machine shop of 35 people would require four days of initial auditing. At a daily rate of $1,400 multiplied by 4, the total cost would be $5,600. There will likely be associated fees that all ISO registrars charge (more info to come in part 2 of this series) and travel expenses may be applied. So, on top of the daily rate you could anticipate $750 - $1,200 additional for a grand total of approximately $6,350 - $6,800. Note that some registrars offer lower fees to smaller businesses or may have local auditors who can drive to your facility at a minimal cost.
Since all IAF member-accredited (International Accreditation Forum) ISO 9001 registrars must follow the “MD-5” document, the audit time allocation and the daily rate are not going to vary much. While fees/travel can mount up, there are ways to mitigate them (this is covered in later parts of the series). Hence, obtaining quotes from any number of registrars will not reveal much difference in the actual cost.
The main costs associated with ISO 9001 certification are those associated with the work performed by the organization. This involves the work put in by key personnel in the development of the quality management system to meet the various ISO 9001:2015 requirements.
Certification of an organization is valid for three years, so to determine the total cost over that period, we should revisit the IAF MD-5 document for guidance. For discussion’s sake, we’ll keep with the example above involving the CNC machine shop with 35 people.
|
Audit Costs
|
Fees & Travel
|
|
Total Cost for ISO 9001 Certification Audit (4 days)
|
$5600
|
$1000
|
$6600
|
1st Year Annual Surveillance Audit (1 day)
|
$1400
|
$1000
|
$2400
|
2nd Year Annual Surveillance Audit (1 day)
|
$1400
|
$1000
|
$2400
|
3rd Year Re-Assessment Audit (2 days)
|
$2800
|
$1000
|
$3800
|
Grand Total(s)
|
$11200
|
$4000
|
$15200
|
After looking at what the total cost would be, one could think about using certification as a qualifier for obtaining sales leads. This could be especially helpful when a purchasing agent only obtains quotes from suppliers who are ISO certified. In this case, an annual average of $2,800 spent on lead generation would be a reasonable value.
To learn more about what’s involved in your organization becoming ISO 9001 certified, stay tuned! Future articles will cover the certification process, choosing a registrar and more.
ISO CERTIFICATION AT THE CENTER
There are two primary benefits associated with being ISO certified: a competitive advantage and the discipline necessary for future growth. Many companies expect their suppliers to have some form of ISO certification. Without this certification, suppliers are unlikely to even be considered. To help companies be successful, The Center’s experts assist manufacturers in integrating their QMS/EMS objectives into their strategic and business plans. Take the first steps in the certification process by
scheduling your free assessment today!
MEET OUR EXPERT: Andy Nichols, Program Manager
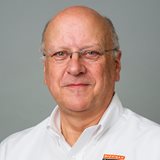
To The Center’s clients, Andy Nichols, CQP FCQI, brings 40 years of expertise in a wide variety of roles and industries, with a particular focus on quality management systems in manufacturing organizations. Prior to joining the Michigan Manufacturing Technology Center, he was the East Coast Regional Sales Manager for NQA, a “Top 5” Global Certification Body, responsible for significant sales growth in a highly competitive marketplace. He has authored three books, “Exploding the Myths Surrounding ISO 9000 – A Practical Implementation Guide” (published by ITG in April 2013) and “A Guide to Effective Internal Management Systems Audits" (published May 2014) and “Implementing ISO 9001:2015 – A practical guide to busting myths surrounding quality management systems” (published October 2022).
Since 1991, the Michigan Manufacturing Technology Center has assisted Michigan’s small and medium-sized businesses to successfully compete and grow. Through personalized services designed to meet the needs of clients, we develop more effective business leaders, drive product and process innovation, promote company-wide operational excellence and foster creative strategies for business growth and greater profitability. Find us at www.the-center.org.
Categories: Quality Management