11/11/2022
BY: CHUCK WERNER
As educators to small and medium-sized businesses on manufacturing technologies, the Michigan Manufacturing Technology Center’s (The Center) Industry 4.0 team participates in trade shows, expositions and technology events, allowing us to interact with experts, suppliers and adopters of technology. We are fortunate to experience current technologies, hear about implementation successes and failures, and get to see the upcoming developments in technology. While some of these new products may never mature into “game-changers” for manufacturing, the fact is that some, if not many, go on to revolutionize the processes and producers of products and services alike.
INNOVATORS OF ADOPTION
Although it would be great if our clients could be “Innovators of Adoption” with regards to technology, we at The Center have learned through our assessments that this is rarely the case, and usually for good reason. Those familiar with our “Adoption Roadmap” model for technology know we start with understanding the Voice of (your) Customer or Voice of (your) Business when identifying a technology to leverage. This is because the application that makes the most sense for a small to medium business to adopt is the one that will address a problem or “pain point” within the business, driving improvement and enhanced profitability.
When considering the Adoption Life Cycle model as seen in the chart below, there are reasons businesses wish to be on the front of the curve. Those who fall into the “Early Adopters” category will enjoy longer benefits of the technology implemented. Those in “Early Majority” will enjoy greater competition by technology suppliers, as well as products tailored to their needs.
Photo: Marketing and Selling High-Tech Products to Mainstream Customers" by Geoffrey A. Moore
Obviously, those in “Late Majority” or “Laggards” put the business at a disadvantage as their competitors are already reaping the rewards of implementation. Essentially, we should agree the best times to consider adoption of a technology is at the front of the curve. Given the widespread difficulties with filling staff vacancies statewide and nationally, now is the time for all manufacturers, and even services providers, to seriously consider automation to address the challenge.
AUTOMATED MATERIAL MOVERS
Improvements in capability, availability and design of cobots places that technology as entering the Early Majority phase of adoption. This is due to the increased number of competitors and the cobot’s ability to meet specific business needs like speed, accuracy, payload and work envelope. With that said, this applies to more than just robots that pick and place, weld, assemble or palletize.
Based on our observations of industry development, another area of robotics that has come of age are the movers of materials and products known as Automated Guided Vehicles (AGVs) and Autonomous Mobile Robots (AMRs). While attending expos and trade shows, it was hard to walk in any direction without bumping into some variety of automated material mover. With this technology, finding a cost-effective option is doable, they can pull a ton and are programmed on a specific path. So, what is the difference between the two?
Using sensors, an AMR is aware of its environment and has the capability to move through determined workspaces independently. The AMR is programmed to move through a pattern or to specific points within the facility, but if the primary path is blocked it can find an alternative path to get where it needs to go, provided it does not travel through any “no go” programmed areas. An AMR costs approximately $30,000.
On the other hand, an AGV follows a provided path using wire, tape or some other device. It can only follow that path and if there is an obstacle in the way, the robot cannot proceed until the obstruction is eliminated. Many AGVs can be purchased for approximately half the price of an AMR.
Both the AMR and AGV can be used to move material, documents and products throughout the workplace without the presence of an associate to enable transportation. In today’s manufacturing landscape, it is difficult to find employees and so we must engage those we have with value-added work as much as possible.
REDUCING WASTE WITH AUTOMATION
Walking (waste of motion) from one area to another or carrying (waste of transportation) things around a business are NOT value-added forms of work. I once performed an assessment at a business that collected and kitted ingredients for hobbyists. It was mentioned that their employees, who were working eight-hour shifts were walking about 13 miles a day. There were four employees performing this type of work on both shifts.
For this example, I will use a base hourly wage of $15 and a burden rate of 24% which brings my total cost per hour to $18.60. If we assume an average speed of 3 miles an hour walking, the daily cost is:
This makes the yearly cost of walking $154,752. Allowing those associates to solely focus on kitting and eliminating even half of that cost would pay for several AGVs (or AMRs), reduce wear and tear on the workers, and still provide a first-year payback.
Of course, the walking data in your business may be less than this example. But are you sure? This form of waste is a large part of what we call the “Hidden Factory” within a company and is commonly dismissed as the cost of doing business. But, once the cost is known, there might be a different opinion of whether it is acceptable or not. And, although there are additional costs for upkeep, charging and upskilling for programming AMRs and AGVs, these robots can reduce the number of lift trucks needed in a facility. This will balance the investment with an overall reduction in maintenance and finding operators for them.
I encourage you to take the time to observe just how much walking is going on around your business. Put a dollar figure on it. Then see if an AGV or AMR is right for keeping your associates engaged in value-added activities.
INDUSTRY 4.0 AT THE CENTER
MEET OUR EXPERT: Chuck Werner, Manager Operational Excellence/Lean Six Sigma Black Belt
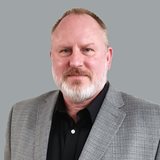
Chuck has been a member of the team at The Center since 2016. His areas of expertise include Lean, Six Sigma and Quality. Chuck has devoted many years to practicing Six Sigma methods, ultimately earning a Six Sigma Master Black Belt in 2011. He is passionate about helping small and medium-sized manufacturers become more prosperous using a variety of tools and methods gathered from over 27 years of experience in manufacturing.
Since 1991, the Michigan Manufacturing Technology Center has assisted Michigan’s small and medium-sized businesses to successfully compete and grow. Through personalized services designed to meet the needs of clients, we develop more effective business leaders, drive product and process innovation, promote company-wide operational excellence and foster creative strategies for business growth and greater profitability. Find us at www.the-center.org.
Categories: Advanced Manufacturing,
Industry 4.0,
Innovation,
Lean Principles,
Manufacturing,
Smart Manufacturing,
Smart Technology,
Technology,
workforce