4/13/2018
BY: MIKE BEELS
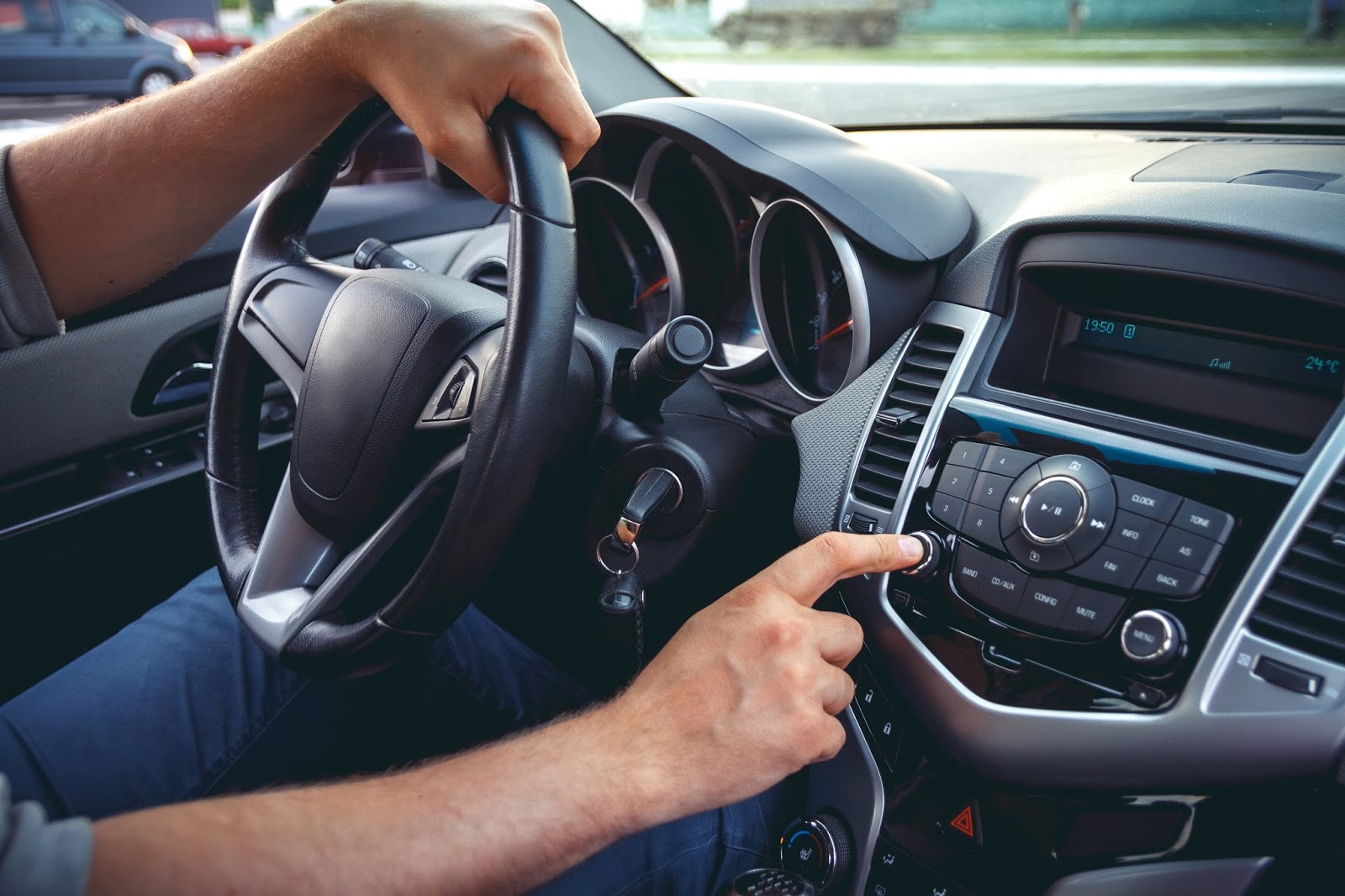
People don’t like change. Learning new ways of doing things and adopting new technology can be a scary proposition. I often have clients ask, “Why do we need to change, we are already working hard?” or, “We are already profitable, why change?” The unfortunate answer is that you cannot avoid change; everything changes over time. Instead of avoiding change out of fear or stubbornness, you must embrace it if you want to keep improving.
Remember when eight-track players were first created, totally revolutionizing the way we listened to music in our cars? What could be better than listening to your favorite music whenever you wanted, instead of waiting for it to come on the radio. We thought it was the peak of individualized listening. Then came cassettes. Then CDs, then MP3s, and now we have Sirius radio and Spotify. What’s next? Only the future knows.
Neglecting to use Spotify may not be as detrimental as neglecting to incorporate changes in your facility, but the point remains the same: you must be able to embrace change. If not, you could be committing professional suicide. In his program titled “The Business of Paradigms,” Joel Barker, a technology and business futurist and the bestselling author, speaks to the fear of making changes in business. His message reminds viewers that even if they are already the leader in their market, someone else can find a better, newer way to produce X at any moment, quickly taking over their spot at the top. If you want to improve your service and remain competitive, innovation is necessary.
Make It Count: 3 Ways to Ensure Change is Successful
Following this initial, monumental step of deciding to change, leaders must then figure out how to incorporate and implement change within their facilities. All change begins and ends with employee support, making employees an integral role in the success of your transformation. When starting any new initiative, first ask yourself the question, “How can I make my employees see the need for change?” Let’s explore the answer to this question by looking at the example of how to successfully transition to a lean culture.
Although there is no magic dust or silver bullet to instantly transform the culture, there are several key elements that can help make this transition effective.
- Leadership is one of the keys to a successful culture transition. Those leading an organization must provide full support to a lean transformation, as they are in charge of commanding the resources. Leaders should be completely committed to this change. If employees can see that it is not a priority for leaders, they will not make it a priority for themselves. Additionally, leaders must commit to this change for the right reasons, not just because “lean” is the latest buzzword or because a customer asked them to do it.
- Communication is another key. Effective communication requires more than an occasional meeting or speech. Nearly every organization tells me, “We don’t communicate!” Between functional silos (engineering, quality, manufacturing, etc.), between departments, between shifts, between hourly and salary employees, there is little to no communication. Lack of sufficient communication among employees and departments will quickly lead to the downfall of a lean culture change. You must communicate why the change is important and, more specifically, how it will affect each worker. If you simply make changes on the shop floor without including all departments in the loop, you will be met with resistance. Employees need to be tuned in to W.I.I.F.M. (What’s In It For Me?) to truly understand and support the need for change. Five-minute stand up meetings and town hall meetings are two commonly used venues for communicating, and each is highly effective. Five-minute stand ups will often include what happened yesterday, what is expected today and what operators need for the future. Town hall meetings are more than just a slideshow on the state of the business. If done correctly, these gatherings not only provide employees with key information, but also provide them the opportunity to bring up issues or questions they have.
- Training is an important aspect that cannot be forgotten. I have witnessed organizations completely fail in their lean transitions because they did not provide lean training for everyone in the organization. Basic training in lean methodologies is necessary for all workers, and should eventually be made part of orientation for new employees. Additionally, as employees begin to participate in kaizen events, more in-depth training will be necessary. For instance, if the kaizen charter called for an event featuring 5S and Visual Management or Single Minute Exchange of Dies (SMED), the participants would need to be trained specifically in those disciplines to be successful.
When considering the move to a leaner environment, you must first ask yourself if your organization is ready to provide the leadership, communication and training necessary. Only then will your organization truly be able to realize success in adapting to change.
MEET OUR EXPERT
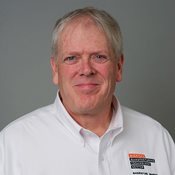
Mike Beels, Lean Program Manager
Mike Beels has served in the role of Lean Program Manager for the Lean Business Solutions Team at The Center for more than 12 years. Mike’s areas of expertise include Change Leadership, Workforce Engagement and Succession Planning, as well as the entire portfolio of Lean strategies and methodologies. He is a professional trainer and has the ability to command an audience and deliver the training message in a way that participants can understand in a clear, non-threatening manner. Mike always leaves trainees excited and ready to complete training transfer to the shop floor or office.
Since 1991, the Michigan Manufacturing Technology Center has assisted Michigan’s small and medium-sized businesses to successfully compete and grow. Through personalized services designed to meet the needs of clients, we develop more effective business leaders, drive product and process innovation, promote company-wide operational excellence and foster creative strategies for business growth and greater profitability. Find us at www.the-center.org.
Categories: Leadership/Culture,
Lean Principles