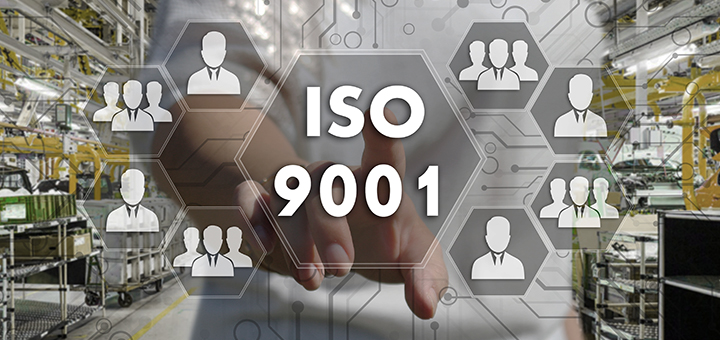
ANSWER from the qms experts:
ISO 9001, the standard for Quality Management Systems, was revised and published in September 2015. Subscribing (or certified) organizations that used the 2008 version have three years (starting from September 2015) to transition to the updated standard. Originally published in 1987 (with revisions in 1994, 2000 and 2008) the 2015 version contains significant changes.
So, what changes are in the new version?
For those familiar with the previous versions of ISO 9001, the most obvious change is the layout of content. The technical committee which drafted the requirements have adopted the ISO Organization's so-called "High Level Structure" also known as "Annex SL." The content contains major changes, too, including:
- The mandate for documentation i.e. quality manuals, procedures or work instructions was omitted. Instead, the organization now decides what it needs in terms of "documented information" (the terminology now used for this aspect)
- The "Process Approach" to implementing a Quality Management System is a clear requirement, rather than having procedures for functions/departments.
- Risk and Opportunity are mentioned throughout the standard (when planning for quality, taking action and considering customers' requirements).
- The requirement for the role of "Management Representative" is missing. Instead, the ownership of the Quality Management System becomes part of the organization's "Leadership."
- Understanding the organization's "Interested Parties," plus those "Internal and External Issues" helps define the "Context of the Organization." After this section, the Quality Policy, Quality Objectives and Scope of the Quality Management System follow.
- The relationship with external sources, e.g., materials, products, services, etc. includes other types of organizations, rather than suppliers, through a traditional purchasing arrangement.
Note: The primary purpose of a Quality Management System is to prevent quality issues from occurring. As a result, the Preventive Action procedure was deleted.
HAVE A QUESTION? CLICK HERE OR EMAIL THE CENTER DIRECTLY AT ISO@THE-CENTER.ORG.